Cálculo de modos de procesamiento y estándares de tiempo
L-4 proporciona recomendaciones para calcular las normas de tiempo para los principales tipos de trabajos de reparación con ejemplos. Los datos de referencia se dan de acuerdo con el libro de referencia L-4. Esto no excluye la posibilidad de utilizar otra literatura de referencia sobre el racionamiento del trabajo de reparación.
Reglamento técnico de trabajos de torneado
Norma de tiempo:
donde T o - tiempo principal (máquina),
L p - longitud estimada de procesamiento, mm. Se determina teniendo en cuenta el tipo de torneado (torneado, mandrinado, corte de extremos, ranurado).
donde l es la longitud de la superficie maquinada según el plano de detalle;
y es el valor del corte y corrida del cortador;
i – número de pases (normalmente i=1);
S p sobre - valor de pasaporte de la alimentación, mm / rev.
Seleccione el avance S p o de acuerdo con las tablas, teniendo en cuenta el material de la pieza, el material de la parte de corte de la herramienta y el acabado requerido.
Para procesar superficies rugosas e intermitentes, reduzca el valor de avance tabular en un 20-35%. Coordine S p sobre con los datos del pasaporte de la máquina (ver Apéndice). Tome S p aproximadamente = ... mm / rev.
N p - valor de pasaporte de la velocidad del eje de la máquina;
seleccione el valor tabular de la velocidad de corte V p t;
asignar factores de corrección:
K m - dependiendo del material de la pieza de trabajo;
K mr - dependiendo del material de la parte de corte de la herramienta;
K x - dependiendo del estado de la superficie tratada;
K oh - dependiendo de la disponibilidad de refrigeración;
Ajustar la velocidad de corte:
V r ck \u003d V r t ∙K m ∙K mr ∙K x ∙K oh;
Determine el valor calculado de la velocidad del husillo de la máquina:
donde D es el diámetro de la pieza de trabajo.
Coordinar con los datos del pasaporte de la máquina n p.
Estaño - tiempo auxiliar, mín.
T en \u003d T en su + T en pr + T en meas, min.
T en su - tiempo auxiliar para la instalación y extracción de la pieza, depende del método de instalación y fijación;
T en pr - tiempo auxiliar para el pasaje;
T in meas - tiempo auxiliar para mediciones, depende del método de medición.
Se asigna cuando hay una transición de medición.
T d - tiempo adicional, min.
Td
donde K es el porcentaje de horas extras. Para trabajos de torneado K=8%;
T pz - tiempo preparatorio y final. Se instala en un lote de piezas, según el tipo de procesamiento y el método de instalación de la pieza;
P p - el tamaño del lote de producción de piezas.
Ejemplo 1 Determine el tiempo de pieza para girar el cuello roscado después de asfaltar en la mangueta del automóvil ZIL-4314.10. El procesamiento se lleva a cabo desde D=42 mm hasta D=36 mm con una longitud de l=32 mm. Equipo: torno de corte de tornillos 1K62.
Información Adicional:
La herramienta de corte es un cortador pasante con una placa de fusión T5K10;
Material procesado - acero 40X;
B c \u003d 400 MPa.
Solución:
1. Profundidad de corte
Número de pasadas i=1.
2. Avance S, mm/rev. con desbaste y profundidad de corte t=3 mm y b c =400 MPa.
Valor de la tabla S t \u003d 0.3-0.6 mm / rev.
De acuerdo con el pasaporte de la máquina S p aproximadamente =0,3 mm / rev.
3. Velocidad de corte V, m/min.
Valor de la tabla V t \u003d 198 m / min.
Corrección de la velocidad de corte:
K m \u003d 1.65 - dependiendo del material que se esté procesando;
K mr \u003d 0.95 - dependiendo del material del cortador;
K x \u003d 0.65 - dependiendo del estado de la superficie tratada;
K oh \u003d 1.0 - dependiendo de la presencia de enfriamiento.
Velocidad de corte corregida:
V p ck \u003d 198 ∙ 1.65 ∙ 0.95 ∙ 0.65 ∙ 1.0 \u003d 201.74 m / min.
4. Velocidad de rotación de la pieza n, rpm:
Según el pasaporte de la máquina n p \u003d 1600 rpm. (ver archivo adjunto)
5. Duración estimada del procesamiento
L p \u003d l + y \u003d 32 + 5 \u003d 37 mm,
donde y=5 mm.
6. Principal (tiempo de la máquina):
7. Tiempo auxiliar.
OFICINA CENTRAL DE NORMAS LABORALES DEL INSTITUTO DE INVESTIGACIÓN CIENTÍFICA DEL TRABAJO
COMITÉ ESTATAL DEL CONSEJO DE MINISTROS DE TRABAJO Y SALARIOS DE LA URSS
Número III
SUJETADORES NORMALIZADOS
Moscú - 1975
OFICINA CENTRAL DE NORMAS LABORALES DEL INSTITUTO DE INVESTIGACIÓN LABORAL DEL COMITÉ ESTATAL DEL CONSEJO DE MINISTROS DE TRABAJO Y SALARIOS DE LA URSS
TIEMPOS TÍPICOS DE CONSTRUCCIÓN DE MÁQUINAS GENERALES para mecanizar piezas de máquinas
Edición 111 TORNILLOS NORMALIZADOS
Normas generales de construcción de maquinaria estándar de tiempo para mecanizado partes de máquina. Problema III. Sujetadores normalizados
Los estándares estándar están destinados a calificadores, tecnólogos y otros trabajadores técnicos y de ingeniería involucrados en el desarrollo de estándares técnicamente sólidos para el procesamiento de sujetadores normalizados en talleres (sitios) de empresas de metalurgia no especializados.
Las normas de tiempo estándar son aprobadas y recomendadas para su uso en empresas por la sección del Consejo de Expertos y Metodología del Banco Central de Ciencia y Tecnología y aprobadas por el Comité Estatal del Consejo de Ministros de Trabajo y Salarios de la URSS (Decreto No. 208 de 15 de agosto de 1972) y acordado con el Consejo Central de Sindicatos de toda la Unión.
La colección fue desarrollada por la Oficina Central de Normas Laborales con la participación de empresas y organizaciones reguladoras de varios ministerios de construcción de maquinaria.
Estos estándares modelo son una edición revisada y complementada de estándares emitidos anteriormente y se introducen para reemplazar la colección de la edición de 1964-1965.
La colección corresponde a la edición de 1975.
Envíe todos los comentarios y sugerencias sobre esta colección a la dirección: 103112, Moscú, KL2, pl. Kuibysheva, 1, TsBNT.
© Instituto de Investigación del Trabajo del Comité Estatal del Consejo de Ministros de la URSS sobre Trabajo y Salarios (Instituto de Investigación del Trabajo), 1975
UNA PARTE COMÚN
Estos estándares de tiempo estándar se recomiendan para estandarizar el trabajo de la máquina en la fabricación de polipastos de ds de fijación normalizados de máquinas en talleres no especializados de empresas de construcción de maquinaria realizadas en tornos, torneado de torreta, taladrado, rectificado y otras máquinas para pequeña escala y Condiciones de producción en masa y en tornos automáticos de un solo husillo, para producción en serie y a gran escala.
Al desarrollar esta colección, la nomenclatura aceptada de piezas se alineó con los requisitos de los GOST revisados y emitidos recientemente.
Con la revisión de las normas estándar de la edición de 1964, la colección se amplió significativamente. Además, se dan los estándares de tiempo para procesar sujetadores en tornos automáticos de un solo husillo. La colección se complementa con mapas para moleteado y calibrado de roscas, rectificado de superficies lisas, procesado de pines, etc.
Los siguientes materiales son la base para el desarrollo de estándares de tiempo estándar:
1. Normas generales de construcción de maquinaria para modos de corte para la regulación técnica del trabajo en máquinas para corte de metales. M., "Ingeniería", 1967.
2. Normas generales de ingeniería para el tiempo auxiliar, para el servicio del lugar de trabajo y el tiempo preparatorio y final cuando se trabaja en máquinas para corte de metales (producción pequeña y única). M., Instituto de Investigación del Trabajo, 1968.
3. Normas generales de ingeniería para el tiempo auxiliar, para el servicio del lugar de trabajo y preparatorias y finales para el reglamento técnico de trabajo de máquinas (producción en serie). M., Instituto de Investigación del Trabajo, 1968.
4. Normas generales de construcción de maquinaria para tiempos y condiciones de corte para trabajos de torneado automático (producción en masa, a gran escala y en serie). M., "Ingeniería", 1971.
Al desarrollar estándares de tiempo estándar, junto con los estándares generales de construcción de máquinas anteriores, se utilizaron los siguientes:
1. GOST para sujetadores (consulte la lista de piezas en la página 20).
2. Procesos tecnológicos, condiciones de corte utilizadas en las empresas y observaciones cronométricas en las condiciones de producción para el tiempo dedicado al procesamiento de sujetadores con máquinas herramienta.
3. Tiempos de fabricación de elementos de fijación industriales y locales.
4. Datos del pasaporte del equipo.
b. Resultados de analisis procesos laborales, el estudio de los métodos racionales de trabajo y la organización del lugar de trabajo.
Los límites de tiempo en la colección se dan en minutos. Los límites de los indicadores numéricos (longitud, diámetro, etc.) para los que se indica "hasta" deben entenderse inclusive.
La colección de normas de tiempo estándar consta de las siguientes secciones:
Una parte común;
Características de los equipos utilizados y tecnología de trabajo;
Organización Laboral;
parte reglamentaria;
Aplicaciones.
Las normas típicas de tiempo para el mecanizado de tornillería son de tipo completo de ampliación, cuando para cada operación se dan las normas de pieza y tiempo preparatorio-final.
Para la conveniencia de usar la colección en los mapas de normas estándar, se da tiempo para el procesamiento completo de las piezas y también se destacan las opciones de procesamiento individuales.
Los tiempos de operación típicos incluyen:
a) tiempo principal (tecnológico);
B) tiempo auxiliar para instalación y remoción de la pieza;
c) tiempo auxiliar asociado a la transición;
d) - tiempo de mantenimiento del lugar de trabajo, descanso y cuidado personal (dentro del 5 al 10% del tiempo operativo, según el tipo de trabajo).
El tiempo parcial por pieza incluye los mismos componentes, con excepción del tiempo auxiliar para instalación y remoción.
El tiempo preparatorio-final en la colección se da en relación a los tipos de máquinas (cuadro 62). Esta vez, prevista para un lote de piezas mecanizadas, prevé el siguiente ámbito de trabajo:
1. Obtención de un pedido y documentación técnica.
2. Familiarización con la obra, dibujos y recepción de instrucciones del maestro.
3. Obtención de herramientas y accesorios, preparación del lugar de trabajo, instalación de equipos, herramientas y accesorios.
4. Eliminación de herramientas y accesorios al final del procesamiento de un lote de piezas, su entrega.
5. Reajuste parcial del equipo en el curso del trabajo.
Los estándares de tiempo típicos están diseñados para las condiciones organizativas y técnicas correspondientes al tipo de producción aceptado. El tamaño del lote de piezas tomadas como una unidad y los factores de corrección por cambios en las condiciones de trabajo se dan después de las tarjetas de tiempo por pieza por tipo de máquina.
Para tornos automáticos monohusillo, el lote de piezas aceptado es superior a 500 piezas.
Si la máquina realiza sistemáticamente el mismo tipo de operaciones en
4
procesamiento de partes estructuralmente similares, el tiempo de pieza dado en estos estándares estándar debe corregirse por el coeficiente / ("0.70.
Los límites de tiempo típicos se calculan para complementar el trabajo con el mantenimiento de una estación. En el caso de mantenimiento de varias máquinas, se deben aplicar normas estándar con coeficientes:
El nivel de productividad laboral adoptado en las normas estándar tiene en cuenta la experiencia del trabajo de los talleres de máquinas de las empresas de construcción de máquinas.
En los casos en que las normas de tiempo vigentes en la empresa sean inferiores a las normas estándar, estas normas de tiempo más progresivas no deben aumentarse.
Con la entrada en vigor de estos modelos de normas, se cancela la colección de la edición de 1964 o 1966.
Al establecer normas de tiempo en las empresas con base en las normas de tiempo estándar de esta colección, la facturación del trabajo debe realizarse de acuerdo con el Libro de Referencia de Tarifa y Calificación Unificada de Trabajos y Profesiones de los Trabajadores, Número 2, aprobado por Decreto del Estado. Comité del Consejo de Ministros de la URSS sobre Trabajo y Salarios y el Consejo Central de Sindicatos de toda la Unión Nº 22 de 21 de enero de 1969, sujeto a adiciones y cambios posteriores.
La discrepancia entre las calificaciones del trabajador y la categoría de trabajo establecida no puede servir de base para ningún cambio en las normas de tiempo en la colección.
Características de los equipos utilizados y tecnología
trabajar
Las características técnicas de las máquinas representativas, los datos de pasaporte, que se tuvieron en cuenta al elegir las condiciones de corte, se presentan en la siguiente tabla.
Las características técnicas y tecnológicas de los modelos de máquina-herramienta anteriores es que cuentan con un conjunto completo de avances, velocidades y potencia suficiente.
Tipo de máquina |
Opciones |
Potencia ■ k*t |
Límites de velocidad de movimiento principal en rpm |
Límites de caída en mm/rev |
|||
Molienda |
5 superficie frontal |
Longitudinal transverso vertical |
|||||
longitudinal transverso vertical |
|||||||
Smolilny |
Diámetro máximo de perforación | ||||||
Krugloshlnfs-eal |
Diámetro máximo de rectificado Longitud máxima de rectificado |
pieza de trabajo 30-235 |
Tabla de velocidades movidas* en m/min 200 - 6000 Avance cruzado del cabezal de molienda en un golpe 0.01-0.02; 0,03-0,01 |
Continuación
Tipo Stayak" |
Opciones |
¡Los límites de velocidad del movimiento principal en aproximadamente! mímica |
Límites de avance en mm/rev |
||||
Máquina de cadera con rodillos sin cuna |
Diámetro de lijado |
más grande el menos | |||||
longitud de la pieza de trabajo |
|||||||
Roscadora semiautomática con cabezal giratorio | (Corte de pernos) | |||||||
Roscadora de rodillos redondos A |
El diámetro más grande del hilo a cortar. | ||||||
Torno monohusillo ga tomate |
El diámetro de procesamiento más grande |
1150 - 7800 800-7670 550-3200 |
Los estándares de tiempo típicos están diseñados para las siguientes tecnologías bajo condiciones:
l pieza de tiempo en las tarjetas está configurado para procesar piezas hechas de aceros al carbono estructurales a * "60-76 kg / mm 2. Cuando se procesan piezas con una herramienta hecha de acero rápido, se proporcionan coeficientes según el grado del material que se está procesando. Al mecanizar piezas con herramientas de carburo, los factores de corrección se dan según la resistencia del material que se está mecanizando.
B. Una pieza de trabajo utilizada para calcular el tiempo de la pieza cuando se procesan piezas en tornos y tornos de torreta, para piezas con un diámetro de hasta 20 mm - una barra de 1000 mm de largo, para piezas con un diámetro de más de 20 mm - una pieza de trabajo separada de productos laminados, estampados o forjados. Al procesar piezas en tornos automáticos de un solo husillo, se toma como pieza de trabajo una barra de 3000 mm de largo.
3. La instalación de piezas se realiza en accesorios universales.
4. Los modos tecnológicos de trabajo en tornos y tornos de torreta para cortadores están diseñados para el uso de herramientas de carburo. Todos los demás tipos de mecanizado (excepto rectificado y laminado de roscas) se realizan con una herramienta de corte de acero rápido. Para el procesamiento automático, las normas también se calculan con la condición de utilizar una herramienta de acero rápido.
6. Los estándares típicos para el procesamiento de pernos, tornillos y tuercas en tornos y torretas se calculan para roscar la clase de precisión 3. En el caso de roscado de 2ª clase, un factor de corrección /("U,2.
<6. В случае изготовления детали ко отдельной заготовки, штамповки или поковки время на отрезку не учитывалось.
7. Los límites de tiempo para el rectificado se calculan en función de la condición de eliminar la tolerancia de 0/1 mm por lado.
8. En las normas de tiempo de pieza, se tiene en cuenta la alineación de pernos y tornillos para procesarlos con alojamiento por el centro del contrapunto en una relación de la longitud de la pieza al diámetro de 8-<10 и рассверливание отверстий в гайках, начиная с диаметра резьбы 30 мм.
9. En el corte de roscas en tornos y torretas, se tiene en cuenta en las normas de tiempo pieza el uso de machos y matrices para diámetros hasta 20 mm y fresas para diámetros superiores a 20 mm.
Organización Laboral
Con una organización racional del trabajo, el lugar de trabajo debe estar equipado de acuerdo con los requisitos del proceso de producción y las condiciones para realizar el trabajo de acuerdo con las normas de saneamiento e higiene y seguridad.
La ubicación de los equipos en el lugar de trabajo, el inventario, el mobiliario industrial, los contenedores, los estantes para los espacios en blanco y los productos terminados se planifica de tal manera que no haya condiciones de trabajo estrechas, costos adicionales, tiempo para caminar y buscar.
El equipamiento del lugar de trabajo debe ser suficiente y correcto. La iluminación requerida está determinada por la naturaleza del trabajo que se está realizando y las normas sanitarias vigentes.
En iluminación natural y artificial, se recomienda colocar los lugares de trabajo de forma que la luz incida a la izquierda o al frente. En presencia de iluminación local, la luz no debe cegar los ojos, la sombra no debe caer sobre la pieza de trabajo.
El diseño exterior de los lugares de trabajo y locales industriales debe cumplir con los requisitos de la estética técnica.
El número de herramientas y accesorios en el lugar de trabajo debe ser ". el mínimo necesario para garantizar un funcionamiento ininterrumpido durante el turno con el menor tiempo necesario para obtenerlos y reemplazarlos.
Las herramientas y los accesorios deben ubicarse en el lugar de trabajo en un orden determinado, conveniente para su uso.
La limpieza de virutas y desechos en el lugar de trabajo la llevan a cabo la producción y los trabajadores, desde los lugares de trabajo, por los limpiadores de las instalaciones de producción del taller.
El número de piezas a procesar, piezas de trabajo en el lugar de trabajo está determinado por el sistema de organización de la producción y debe garantizar la operación continua durante el turno.
En el lugar de trabajo, hay un mapa instructivo y operativo para elegir la erisipela en corte de acuerdo con el tipo desarrollado por la planta Nevsky machine-cTpoH \ v .. oHWM que lleva el nombre. V. I. Lenin o PKTImash (ver Apéndice 2).
A continuación se presentan algunos esquemas para organizar trabajos para operadores de máquinas, teniendo en cuenta los requisitos para organizar trabajadores en el condado.
Esquema de la organización del lugar de trabajo de un tornero.

/ - mesita de noche instrumental; 2 - tableta para colgar dibujos; 3 - mesa de recepción; 4 - celosía para piernas
El lugar de trabajo del tornero está equipado con un armario de herramientas para el trabajo en dos turnos (ver Fig. 7), en cada distancia del cual se almacena un conjunto permanente de herramientas y equipos para el cuidado del equipo, así como una mesa de recepción (ver Fig. 8).
1 - mesita de noche instrumental; 2 - tableta para colgar dibujos de piezas de trabajo; 3 - celosía para piernas; 4 - mesa de recepción; 5 - estante para almacenamiento horizontal de barras
El lugar de trabajo del revólver está equipado con un gabinete de herramientas instalado a la derecha para el trabajo en dos turnos (<см. рис. 7), приемным столиком (ом. рис. 8), установленным слева.
Se instala un contenedor para piezas terminadas en la placa superior de la mesa de recepción; el estante inferior puede almacenar accesorios para la máquina. Si (la máquina de torreta está diseñada para el procesamiento de barras y cartuchos, entonces el contenedor en rack con espacios en blanco se coloca en un lugar vacío detrás del gabinete de herramientas. Para las máquinas de torreta destinadas solo al procesamiento de mandril, se instalan dos contenedores en la mesa de recepción (para espacios en blanco y para piezas terminadas); y el stock de espacios en blanco en la estela y el contenedor de engorde está ubicado a la derecha del trabajador detrás del gabinete de herramientas.
El lugar de trabajo del perforador está equipado con un armario de herramientas para trabajo en dos turnos (ver Fig. 7), en cada compartimento del cual hay un juego permanente de herramientas y una mesa de recepción (ver Fig. 8), ubicada a la izquierda. En el estante inferior de la mesa de recepción se almacenan pequeños dispositivos.
Esquema de organización del lugar de trabajo de un revólver.

Esquema de la organización del lugar de trabajo de un perforador que trabaja en una máquina de perforación vertical
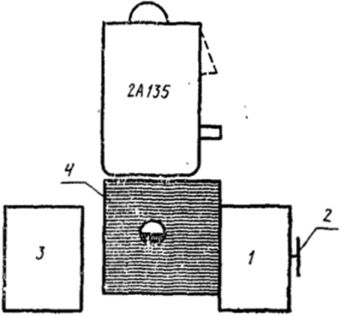
1 - armario de herramientas. Cuota; 2 tabletas para colgar dibujos de piezas de trabajo; 3 - mesa de recepción; rejilla de 4 pies
El conjunto de herramientas necesarias para el trabajo directo se coloca en el estante superior de la mesita de noche.
Esquema de la organización del lugar de trabajo de la fresadora.

/ - mesita de noche instrumental; 2-. placa para colgar dibujos de piezas de trabajo; 3 - mesa de recepción; 4 - celosía para piernas; 5 estantes para luminarias y accesorios; 6 - cremallera para mandriles y barras de mandrinar
El lugar de trabajo del molinero está equipado con un armario de herramientas para trabajo en dos turnos (om. Fig. 7), en cada compartimento en el que se almacenaba un juego permanente de herramientas.
A la derecha del trabajador se instala la mesita de noche y a la izquierda se coloca una mesa de recepción (ver Fig. 8) para dos contenedores. Los aditamentos y accesorios para la máquina se colocan en un estante con una plataforma deslizante (ver Fig. 9) instalada detrás de la máquina.
Con un mayor stock de piezas destinadas al procesamiento, se colocan en un contenedor de estantes o en paletas en la parte posterior de la máquina.
Esquema de la organización del lugar de trabajo del molinillo.

1 - mesa de recepción con cajas de herramientas; 2 - mesa de recepción móvil; 3 tabletas para colgar dibujos de piezas de trabajo; 4-dispositivo de equilibrio para un grupo de máquinas
Cuando se trabaja con una herramienta abrasiva, las reglas de seguridad e higiene industrial no permiten su almacenamiento a largo plazo en el lugar de trabajo, por lo tanto, solo los accesorios de la máquina y una herramienta de medición universal se incluyen en el conjunto permanente de la herramienta de la amoladora.
En base a esto, el lugar de trabajo de la amoladora no está equipado con un gabinete de herramientas, sino con una mesa de recepción con cajas de herramientas (el número de cajas se determina en cada caso específico), en el que se almacena un conjunto de herramientas (ver Fig. 10).
Para mayor comodidad, el lugar de trabajo de la amoladora está equipado con una mesa de recepción móvil (ver Fig. III), en la que se coloca la herramienta necesaria para el trabajo.
Esquema del diseño del área de procesamiento automático.
/ - máquina de torno de un solo husillo 1A-Sh8; 2 - máquina de torno de un solo husillo 1A124; 3 - mesa de recepción; 4 - "mesa de recepción con cajas de herramientas; 5 estantes para almacenamiento horizontal de barras; 6 - gabinete de ajuste
Típico de las secciones automáticas es el mantenimiento de varias máquinas y el ajuste del equipo por parte de un ajustador. Por lo tanto, en las secciones de bocanadas automáticas, no se equipa un lugar de trabajo separado, sino el sitio en su conjunto. El área descrita está equipada con un armario de montaje (ver Fig. 12), mesas de recepción (ver Fig. 8, 10) y estantes para almacenar barras (ver Fig. 10).
Las mesas de recepción están diseñadas para colocar sobre ellas contenedores con las piezas acabadas y el útil de medición que sea directamente necesario en la obra (calibres, plantillas, etc.). El contenedor con las piezas terminadas se traslada al lugar de trabajo del Departamento de Control de Calidad utilizando un yura-beam. El número de barras que necesita un trabajador para un turno se alimenta a la máquina antes del comienzo del turno. Las barras se colocan sobre bastidores formados por dos o tres tramos conectados entre sí. La ubicación de los bastidores está determinada por el diseño del equipo y la conveniencia de volver a llenar las barras en la máquina.
Una de las mesas de recepción en un grupo de máquinas atendidas por un trabajador tiene cajas de herramientas en las que el trabajador almacena las herramientas necesarias.
Equipamiento organizativo de los lugares de trabajo.
La mesita de noche está diseñada para almacenar las herramientas necesarias en los lugares de trabajo de los operadores de máquinas, documentación y productos para el cuidado de equipos.
Cada compartimento de la mesita de noche se cierra con una puerta y se asigna a un trabajador. Los compartimentos disponen de cajas de herramientas y baldas para guardar documentación, accesorios y enseres no negritas, engrasadores, material de limpieza, etc.
El estante superior de la mesita de noche se puede cubrir con plástico. En los soportes se fija una placa extraíble para la fijación de dibujos y un proceso tecnológico, de plástico decorativo laminado en madera.
Mesa de recepción
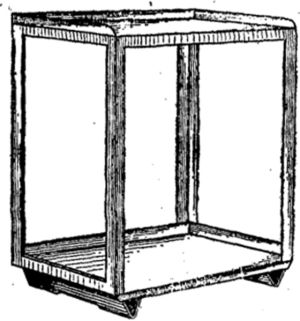
En el estante superior de la mesa hay un contenedor con piezas procesadas o las piezas mismas. Si es necesario, los accesorios y accesorios se pueden almacenar en el estante inferior.
En lugares de trabajo individuales, la mesa se puede utilizar para colocar sobre ella la herramienta utilizada en el trabajo.
Porta accesorios con plataforma extraíble
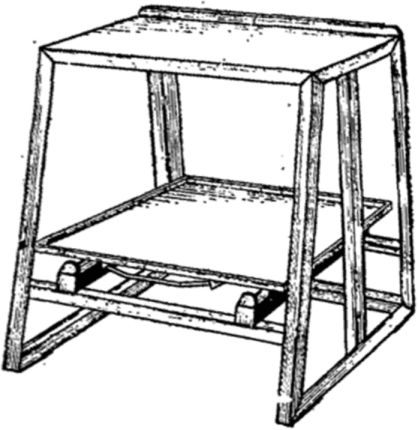
La plataforma se desplaza sobre rodillos y dispone de limitador de carrera. Los detalles del bastidor están hechos de perfil doblado y chapa de acero. El estante superior y la plataforma están hechos de madera impregnada con resina de fenol-formaldehído.
Mesa de recepción con cajas de herramientas.
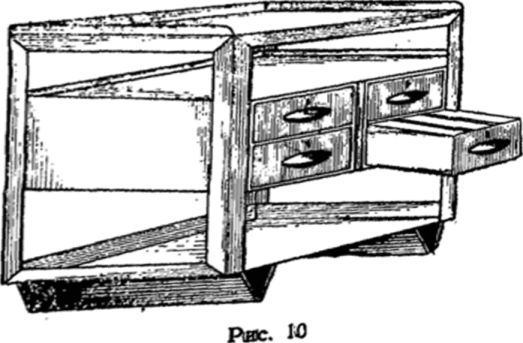
CAJÓN DE ESCRITORIO Se utiliza para almacenar herramientas y el estante superior para colocar contenedores con piezas o para disponer las herramientas necesarias para el trabajo.
El diseño prevé la posibilidad de instalar dos o cuatro * cajas de herramientas gyreh. Al instalar cuatro cajones, dos de ellos se colocan en una percha con rieles, bolas y bastidores adjuntos.
Las cajas se mueven fácilmente sobre rodillos y tienen limitador de recorrido. se pueden instalar tabiques regulables, formando celdas y del tamaño deseado. Entre el estante superior y los cajones hay espacio para documentación técnica. En la parte posterior de la mesa hay soportes para montar la tableta de documentación. Las piezas de Olika están hechas de perfil doblado y chapa de acero.
Mesa de recepción móvil
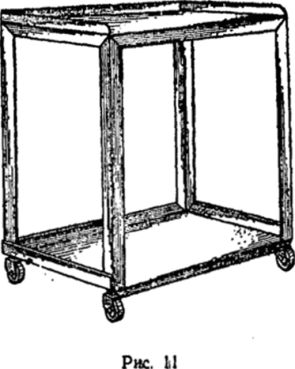
La mesa se utiliza en aquellos puentes de trabajo donde, debido a las condiciones de trabajo, los equipos de oficina estacionarios (armarios de herramientas o mesas de recepción) no pueden instalarse lo suficientemente cerca y convenientemente cerca de la máquina.
En los estantes superior e inferior de la mesa, el trabajador coloca la herramienta que necesita en su trabajo y coloca la mesa en el lugar más conveniente para él. Los detalles de la mesa son de perfil doblado y chapa de acero. Si es necesario, la mesa puede equiparse con un asa para facilitar el movimiento.
Armario

Arroz. No.
El armario consta de elementos individuales (base, brazo y estantes traseros, puertas, cajones de almacenamiento y estantes). Los estantes se pueden volver a guardar pero a la altura. Los tabiques ajustables se pueden instalar en cajones y estantes, formando celdas del tamaño deseado. Para acomodar una herramienta larga en la cavidad de las puertas, una. titulares distantes.
Estantería para almacenaje horizontal de barras
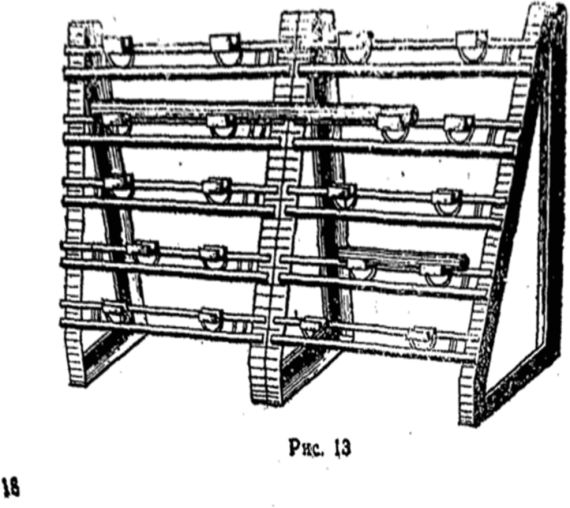
El rack dispone de cinco carriles situados a diferentes alturas, sobre los que se fijan unos soportes móviles.
Las varillas se colocan sobre soportes, cuya ubicación y número se determina en cada caso por separado. El diseño prevé la posibilidad de conectar secciones de cremallera a lo largo de la longitud. En la fig. 13 muestra dos secciones conectadas entre sí.
Los detalles del estante están hechos de un perfil doblado y una esquina. El prisma de apoyo está fabricado en madera impregnada con resina de fenol-formaldehído.
2.8.1 Racionamiento de operaciones en máquinas universales con mando manual.
Definición del tiempo principal (tecnológico).
El tiempo principal está determinado por las fórmulas de cálculo para el tipo de trabajo correspondiente y para cada transición tecnológica (T o1, T o2, ..., T o n).
El tiempo principal (tecnológico) para la operación:
donde n es el número de transiciones tecnológicas.
Definición de tiempo auxiliar.
Para equipos diseñados para realizar trabajos de transición simple con modos constantes en una sola operación (máquinas de corte múltiple, hidrocopiadoras, talladoras de engranajes, brochadoras, roscadoras), se da el tiempo auxiliar T para la operación, incluido el tiempo para instalar y quitar el pieza de trabajo
El tiempo auxiliar para la operación está determinado por la fórmula:
donde t boca - el tiempo para instalar y quitar la pieza, dado por tipo de accesorio, independientemente de los tipos de máquinas, min;
t carril: el tiempo asociado con la transición, dado por tipos de máquinas, min;
t' carril - tiempo no incluido en el complejo de tiempo asociado a la transición, min;
t meas - tiempo para las mediciones de control después del final del tratamiento superficial. El tiempo de las medidas de control se incluye solo en aquellos casos en que no se superpone con el tiempo principal o no se incluye en el complejo de tiempo asociado a la transición, min;
Kt in - factor de corrección para el tiempo auxiliar, min.
Definición de tiempo operativo:
, min
donde T sobre - el tiempo principal para el procesamiento;
T en - tiempo auxiliar para el procesamiento, min.
Determinación del tiempo para el mantenimiento del lugar de trabajo y necesidades personales.
El tiempo para el mantenimiento del lugar de trabajo, el descanso y las necesidades personales se determina como un porcentaje del tiempo operativo de acuerdo con los libros de referencia normativos.
Tiempo estándar:
donde α obs y α voln son el tiempo de servicio al lugar de trabajo y el tiempo de descanso y necesidades personales, expresado como porcentaje del tiempo operativo.
Definición de tiempo preparatorio-final.
El tiempo preparatorio y final T pz se normaliza para un lote de piezas, y parte de él por pieza se incluye en el tiempo de cálculo de piezas:
, min
donde n d es el número de partes en el lote.
2.8.2 Normalización de operaciones en máquinas CNC universales y polivalentes.
La norma del tiempo y sus componentes:
, min
donde T tsa - el tiempo de ciclo de la operación automática de la máquina según el programa, min.
, min
donde T o - el tiempo principal (tecnológico) para procesar una parte está determinado por la fórmula:
, min
donde L i es la longitud de la trayectoria recorrida por la herramienta o pieza en la dirección de avance al procesar la i-ésima sección tecnológica (teniendo en cuenta el hundimiento y el rebasamiento), mm;
S mi - minuto de alimentación en la i-ésima sección tecnológica, mm/min;
Tm-v: tiempo auxiliar de la máquina según el programa (para suministrar una pieza o herramienta desde los puntos de inicio a las zonas de procesamiento y retracción, ajuste de la herramienta a un tamaño, cambio de herramienta, cambio de magnitud y dirección de avance), el tiempo de pausas tecnológicas, min.
, min
donde T v.y es el tiempo de instalación y desmontaje de la pieza manualmente o con elevador, min;
T v.op - tiempo auxiliar asociado a la operación (no incluido en el programa de control), min;
Т v.meas – tiempo auxiliar sin superposición para mediciones, min;
K t in: factor de corrección para el tiempo de realización de trabajos auxiliares manuales, según el lote de piezas de trabajo;
α tech, α org, α otd: tiempo para el mantenimiento técnico y organizativo del lugar de trabajo, para el descanso y las necesidades personales para el servicio de ventanilla única, % del tiempo operativo.
La norma de tiempo para configurar la máquina se presenta como el tiempo para el trabajo preparatorio y final en el procesamiento de lotes de piezas, independientemente del tamaño del lote, y está determinada por la fórmula:
donde T p-31 - la norma de tiempo para recibir un pedido, documentación tecnológica al comienzo del trabajo y entrega al final del turno, min; Tp-31 = 12 min;
T p-32: la norma de tiempo para configurar una máquina, accesorio, herramienta, dispositivos de software, min;
T pr.arr - la norma de tiempo para el procesamiento de prueba (de la primera parte), min.
Reglamento técnico.
Se realiza la normalización técnica para la operación 005 "Torno con PU" y la operación 030 "Complejo con PU".
1. Operación 005 "Torneado con PU".
1.1 El principal tiempo de procesamiento (tecnológico) para cada transición está determinado por la fórmula:
, min
, min
donde l corte - longitud de corte, mm
y, ∆ - valor de penetración o sobremarcha, mm
L es la longitud de la trayectoria de la parte de corte de la herramienta, mm.
L 1 \u003d (113-70) / 2 + (65-33) / 2 + 4 \u003d 42 mm;
L 2 \u003d 35 + 5 +2 + 4 + 2.5 + 4 \u003d 57 mm;
L 3 \u003d (113-70) / 2 + 4 \u003d 11 mm;
L 4 \u003d 57 + 4 \u003d 61 mm;
L 5 \u003d 57 + 4 + 1 + 4 \u003d 66 mm.
T o1 \u003d 42 / (0.6 × 315) \u003d 0.22 min;
T o2 \u003d 51 / (0.6 × 500) \u003d 0.27 min;
T o3 \u003d 11 / (0.15 × 500) \u003d 0.14 min;
T o4 \u003d 61 / (0.3 × 800) \u003d 0.25 min;
A 5 \u003d 66 / (0.15 × 1250) \u003d 0.35 min.
1.2 El tiempo de procesamiento principal por operación está determinado por la fórmula.