ЦЕНТРАЛНО БЮРО ПО ТРУДОВИ НОРМИ КЪМ НАУЧНОИЗСЛЕДОВАТЕЛСКИ ИНСТИТУТ ПО ТРУДА
ДЪРЖАВЕН КОМИТЕТ НА МИНИСТЕРСКИЯ СЪВЕТ НА СССР ПО ТРУДА И ЗАПЛАТИТЕ
Брой III
НОРМАЛИЗИРАНИ КРЕПЕЖИ
Москва - 1975 г
ЦЕНТРАЛНО БЮРО ПО ТРУДОВИ СТАНДАРТИ КЪМ ИНСТИТУТА ПО ТРУДОВИ ИЗСЛЕДВАНИЯ НА ДЪРЖАВНИЯ КОМИТЕТ НА МИНИСТЕРСКИЯ СЪВЕТ НА СССР ПО ТРУДА И ЗАПЛАТИТЕ
ОБЩИ МАШИНОСТРОИТЕЛНИ ТИПИЧНИ НОРМИ ЗА ВРЕМЕ за обработка на машинни части
Брой 111 НОРМАЛИЗИРАНИ КРЕПЕЖИ
Общи машиностроителни нормативи за време за обработка на машинни части. Брой III. Нормализирани крепежни елементи
Стандартните стандарти са предназначени за оценители, технолози и други инженерни и технически работници, участващи в разработването на технически издържани стандарти за обработка на нормализирани крепежни елементи в неспециализирани металообработващи цехове (обекти) на предприятия.
Нормите за стандартно време са одобрени и препоръчани за използване в предприятията от секцията на Експертния и методически съвет на Централната банка за наука и технологии и одобрени от Държавния комитет на Съвета на министрите на СССР по труда и заплатите (Постановление № 208 от 15 август 1972 г.) и съгласувано с Всесъюзния централен съвет на профсъюзите.
Колекцията е разработена от Централното бюро по трудови стандарти с участието на предприятия и регулаторни организации на различни министерства на машиностроенето.
Тези типови стандарти са преработено и допълнено издание на предишни издадени стандарти и са въведени, за да заменят колекцията от изданието от 1964-1965 г.
Сборникът отговаря на изданието от 1975 г.
Моля, изпращайте всички коментари и предложения за тази колекция на адрес: 103112, Москва, KL2, pl. Куйбишева, 1, ЦБНТ.
© Изследователски институт по труда на Държавния комитет на Съвета на министрите на СССР по труда и заплатите (Научноизследователски институт по труда), 1975 г.
ОБЩА ЧАСТ
Тези стандартни времеви стандарти се препоръчват за стандартизиране на машинната работа при производството на нормализирани закрепващи ds-подемници на машини в неспециализирани цехове на машиностроителни предприятия, извършвани на стругове, стругове, пробивни, шлифовъчни и други машини за дребномащабни и условия на масово производство и на едношпинделни автоматични стругове - за серийно "и широкомащабно производство.
При разработването на тази колекция приетата номенклатура на частите беше приведена в съответствие с изискванията на новоиздадените и ревизирани GOSTs.
С преразглеждането на стандартните норми от изданието от 1964 г. колекцията беше значително разширена. Освен това са дадени стандартите за време за обработка на крепежни елементи на едношпинделни автоматични стругове. Колекцията е допълнена с карти за нарязване и калибриране на резби, шлайфане на гладки повърхности, обработка на щифтове и др.
Следните материали са в основата на разработването на стандартни времеви стандарти:
1. Общи машиностроителни стандарти за режими на рязане за техническо регулиране на работата на металорежещи машини. М., "Инженерство", 1967 г.
2. Общи инженерни норми за спомагателно време, за обслужване на работното място и подготвително и заключително време при работа на металорежещи машини (дребномащабно и единично производство). М., Изследователски институт по труда, 1968 г.
3. Общи инженерни стандарти за спомагателно време, за обслужване на работното място и подготвителни и заключителни за техническото регулиране на машинната работа (серийно производство). М., Изследователски институт по труда, 1968 г.
4. Общи машиностроителни норми за време и условия на рязане за автоматична стругова работа (масово, едросерийно и серийно производство). М., "Инженерство", 1971 г.
При разработването на стандартни времеви стандарти, заедно с горните общи стандарти за машиностроене, бяха използвани следните:
1. GOSTs за крепежни елементи (вижте списъка на частите на страница 20).
2. Технологични процеси, условия на рязане, използвани в предприятията и хронометрични наблюдения в производствени условия за времето, прекарано в машинната обработка на крепежни елементи.
3. Промишлени и местни времена за производство на крепежни елементи.
4. Паспортни данни за оборудване.
b. Резултати от анализа трудови процеси, изучаване на рационални методи на труд и организация на работното място.
Сроковете в сборника са дадени в минути. Границите на цифровите показатели (дължина, диаметър и т.н.), за които е посочено "до", трябва да се разбират включително.
Колекцията от норми за стандартно време се състои от следните раздели:
Обща част;
Характеристика на използваната техника и технология на работа;
Организация на труда;
Регулативна част;
Приложения.
Типичните норми на време за обработка на крепежни елементи са пълен тип уголемяване, когато за всяка операция са дадени нормите на парче и подготвително-крайно време.
За удобство при използване на колекцията в картите на стандартните норми е дадено време за пълна обработка на частите, а също така са подчертани индивидуалните опции за обработка.
Типичните работни времена включват:
а) основно (технологично) време;
б) спомагателно времеза монтаж и демонтаж на детайла;
в) спомагателно време, свързано с прехода;
г) - време за поддръжка на работното място, почивка и лични грижи (в рамките на 5 до 10% от оперативното време в зависимост от вида на работата).
Частичното време включва същите компоненти, с изключение на допълнителното време за монтаж и демонтаж.
Подготвителен крайно времев колекцията е дадена във връзка с видовете металорежещи машини (графика 62). Това време, зададено за партида обработени части, осигурява следния обхват на работа:
1. Получаване на поръчка и техническа документация.
2. Запознаване с работата, чертежите и получаване на инструкции от майстора.
3. Получаване на инструменти и приспособления, подготовка на работното място, настройка на оборудване, инструменти и приспособления.
4. Отстраняване на инструменти и приспособления в края на обработката на партида от части, тяхната доставка.
5. Частична пренастройка на оборудването в процеса на работа.
Типичните времеви стандарти са предназначени за организационни и технически условия, съответстващи на приетия тип производство. Размерът на партидата детайли, взети като единица, и корекционните коефициенти за променените условия на работа са дадени след картите за часово време по части по вид машина.
За едношпинделни автоматични стругове приетата партида от части е повече от 500 бр.
Ако машината извършва систематично един и същи тип операции на
4
обработка на структурно подобни части, време на парче, дадени в тези стандартни норми, трябва да се коригират с коефициента /("0,70.
Типичните срокове се изчисляват, за да допълнят работата с поддръжка на една станция. В случай на многомашинна поддръжка трябва да се прилагат стандартни норми с коефициенти:
Нивото на производителност на труда, прието в стандартните норми, отчита опита от работата на машинните цехове на машиностроителните предприятия.
В случаите, когато действащите норми за време в предприятието са по-малки от стандартните норми, тези по-прогресивни норми за време не трябва да се увеличават.
С влизането в сила на тези типови стандарти колекцията от изданието от 1964 или 1966 г. се отменя.
При установяване на времеви норми в предприятия въз основа на стандартните времеви норми от тази колекция, таксуването на труда трябва да се извършва съгласно Единния тарифен и квалификационен справочник на работите и професиите на работниците, брой 2, одобрен с Указ на Държавния Комитетът на Съвета на министрите на СССР по труда и заплатите и на Всесъюзния централен съвет на профсъюзите № 22 от 21 януари 1969 г. с последващи допълнения и промени в него.
Несъответствието между квалификацията на работника и установената категория труд не може да послужи като основание за промени в нормите за време в колекцията.
Характеристики на използваната техника и технология
работа
Техническите характеристики на представителните машини, паспортните данни, които са взети предвид при избора на условия на рязане, са представени в таблицата по-долу.
Техническите и технологичните характеристики на горните модели металорежещи машини са, че те имат пълен набор от подавания, скорости и достатъчна мощност.
Тип машина |
Настроики |
Мощност ■ k*t |
Основни ограничения на скоростта на движение в rpm |
Граници на падане в mm/rev |
|||
Фрезоване |
5 предна повърхност |
Надлъжно напречен вертикален |
|||||
надлъжно напречен вертикален |
|||||||
Смолилен |
Максимален диаметър на пробиване | ||||||
Круглошлнфс-еал |
Максимален диаметър на смилане Максимална дължина на смилане |
детайл 30-235 |
Скорости на движение* таблица в m/min 200 - 6000 Напречно подаване на шлифовъчната глава в един ход 0,01-0,02; 0,03-0,01 |
Продължение
Тип Стаяк" |
Настроики |
Ограниченията на скоростта на основното движение в около! мим |
Граници на подаването в mm/rev |
||||
Машина без люлка и валяк |
Диаметър на шлайфане |
най велик най-малко | |||||
дължина на детайла |
|||||||
Резбонарезна полуавтоматична машина с въртяща се глава | (Болторезна) | |||||||
Резбонарезна машина с кръгли ролки A |
Най-големият диаметър на резбата, която ще се нарязва | ||||||
Едношпинделен струг ga tomato |
Най-големият диаметър на обработка |
1150 - 7800 800-7670 550-3200 |
Типичните времеви стандарти са предназначени за следните технологии при условия:
L. Частичното време в картите е зададено за обработка на детайли от структурни въглеродни стомани a * "60-76 kg / mm 2. При обработка на части с инструмент, изработен от бързорежеща стомана, се предоставят коефициенти в зависимост от степента на обработвания материал. При обработка на части с твърдосплавни инструменти се дават корекционни коефициенти в зависимост от якостта на обработвания материал.
Б. Заготовка, използвана за изчисляване на времето за обработка на детайли на стругове и револверни стругове, за части с диаметър до 20 mm - прът с дължина 1000 mm, за части с диаметър над 20 mm - отделен детайл от валцувани продукти, щамповане или коване. При обработка на детайли на едношпинделни автоматични стругове като детайл се взема прът с дължина 3000 mm.
3. Монтирането на части се извършва в универсални приспособления.
4. Технологичните режими на работа на стругове и револверни стругове за фрези са предназначени за използване на твърдосплавни инструменти. Всички останали видове обработка (с изключение на шлайфане и навиване на резба) се извършват с режещ инструмент, изработен от бързорежеща стомана. За автоматична обработка нормите се изчисляват и при условие за използване на инструмент от бързорежеща стомана.
6. Типичните стандарти за обработка на болтове, винтове и гайки на стругове и револвери се изчисляват за резбоване на 3-ти клас на точност. В случай на резба от 2-ри клас, корекционен коефициент /("U,2.
<6. В случае изготовления детали ко отдельной заготовки, штамповки или поковки время на отрезку не учитывалось.
7. Времевите граници за шлайфане се изчисляват въз основа на условието за премахване на надбавката от 0/1 mm на страна.
8. В нормите на работното време подравняването на болтовете и винтовете се взема предвид за обработката им с подаване от центъра на задната част при съотношение на дължината на детайла към диаметъра 8-<10 и рассверливание отверстий в гайках, начиная с диаметра резьбы 30 мм.
9. При рязане на резби на стругове и револвери използването на метчици и матрици за диаметри до 20 mm и фрези за диаметри над 20 mm се вземат предвид в нормите на работното време.
Организация на труда
При рационална организация на труда работното място трябва да бъде оборудвано в съответствие с изискванията на производствения процес и условията за извършване на работа при спазване на правилата за санитария, хигиена и безопасност.
Разположението на оборудването на работното място, инвентара, промишлените мебели, контейнерите, стелажите за заготовки и готовите продукти е планирано по такъв начин, че да няма тесни условия на работа, допълнителни разходи, време за ходене и търсене.
Оборудването на работното място трябва да е достатъчно и правилно. Необходимото осветление се определя от естеството на извършваната работа и действащите санитарни стандарти.
При естествено и изкуствено осветление се препоръчва работните места да се поставят така, че светлината да пада отляво или отпред. При наличие на локално осветление светлината не трябва да заслепява очите, сянката не трябва да пада върху детайла.
Външният дизайн на работните места и производствените помещения трябва да отговаря на изискванията на техническата естетика.
Броят на инструментите и приспособленията на работното място трябва да бъде ". минимумът, необходим за осигуряване на непрекъсната работа по време на смяната с най-малко време, изразходвано за тяхното получаване и подмяна.
Инструментите и приспособленията трябва да бъдат разположени на работното място в определен ред, удобен за използване.
Почистването на чипове и отпадъци на работното място се извършва от производство и работници, от работните места - от чистачи на цехови производствени съоръжения.
Броят на детайлите за обработка, заготовките на работното място се определя от системата за организация на производството и трябва да осигурява непрекъсната работа по време на смяната.
На работното място има инструктивна и оперативна карта за избор на еризипел при рязане според типа, разработен от Nevsky machine-cTpoH \ v .. oHWM завод на името на. V. I. Lenin или PKTImash (виж Приложение 2).
По-долу са дадени някои схеми за организиране на работа на машинни оператори, като се вземат предвид изискванията за организация на работниците в окръга.
Схема на организацията на работното място на стругар

/ - инструментално нощно шкафче; 2 - таблет за окачване на рисунки; 3 - приемна маса; 4 - решетка за крака
Работното място на стругаря е оборудвано с инструментален шкаф за двусменна работа (виж фиг. 7), на всяко разстояние от което се съхранява постоянен набор от инструменти и оборудване за грижа за оборудването, както и приемна маса (виж фиг. 8).
1 - инструментално нощно шкафче; 2 - таблет за окачване на чертежи на детайли; 3 - решетка за крака; 4 - приемна маса; 5 - стелаж за хоризонтално съхранение на пръти
Работното място на револвера е оборудвано с монтиран вдясно от него шкаф за инструменти за работа на две смени (<см. рис. 7), приемным столиком (ом. рис. 8), установленным слева.
На горната плоча на приемната маса е монтиран контейнер за готови части; долният рафт може да съхранява аксесоари за машината. Ако (револверната машина е предназначена за обработка на пръти и патрони, тогава стелажният контейнер със заготовки се поставя на празно място зад шкафа с инструменти. За револверни машини, предназначени само за обработка на патронници, два контейнера са монтирани на приемната маса (за заготовки и за готови части); и запасът от заготовки в стелата и контейнера за угояване се намира отдясно на работника зад шкафа с инструменти.
Работното място на пробивника е оборудвано с инструментален шкаф за двусменна работа (виж фиг. 7), във всяко отделение на който има постоянен набор от инструменти, и приемна маса (виж фиг. 8), поставена отляво. На долния рафт на приемната маса се съхраняват малки устройства.
Схема за организиране на работното място на револвер

Схема на организацията на работното място на бормашина, работеща на вертикална пробивна машина
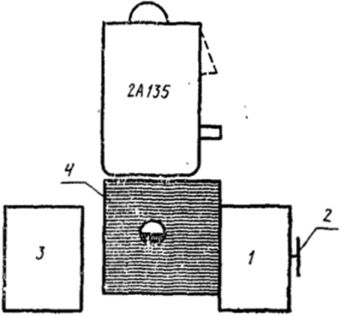
1 - шкаф за инструменти. дял; 2-таблетка за окачване на чертежи на детайли; 3 - приемна маса; 4 фута решетка
Комплектът инструменти, необходими за директна работа, е поставен на горния рафт на нощното шкафче.
Схема на организацията на работното място на фрезата

/ - инструментално нощно шкафче; 2-. табела за окачване на чертежи на детайли; 3 - приемна маса; 4 - решетка за крака; 5-стойка за приспособления и аксесоари; 6 - стелаж за дорници и бормашини
Работното място на мелничаря е оборудвано с инструментален шкаф за двусменна работа (om. Фиг. 7), във всяко отделение на който се съхранява постоянен набор от инструменти.
Нощното шкафче е монтирано отдясно на работника, а приемната маса е поставена отляво (виж фиг. 8) за два контейнера. Приспособленията и аксесоарите за машината са поставени върху стелаж с плъзгаща се платформа (виж фиг. 9), монтирана зад машината.
При увеличен запас от части, предназначени за обработка, те се поставят в стелажен контейнер или на палети на гърба на машината.
Схема на организацията на работното място на мелницата

1 - приемна маса с кутии за инструменти; 2 - подвижна приемна маса; 3-таблетка за окачване на чертежи на детайли; 4-балансиращо устройство за група машини
При работа с абразивен инструмент правилата за безопасност и промишлена хигиена не позволяват дългосрочното му съхранение на работното място, поради което в постоянния комплект на инструмента за мелница са включени само машинни принадлежности и универсален измервателен инструмент.
Въз основа на това работното място на мелницата е оборудвано не с шкаф за инструменти, а с приемна маса с кутии за инструменти (броят на кутиите се определя за всеки конкретен случай), в който се съхранява набор от инструменти (виж фиг. 10).
За удобство работното място на мелницата е оборудвано с подвижна приемна маса (виж фиг. III), върху която се поставя необходимият за работа инструмент.
Схема на оформлението на зоната за автоматична обработка
/ - едношпинделна стругова машина 1А-Ш8; 2 - струг едношпинделна машина 1A124; 3 - приемна маса; 4 - "получаваща маса с кутии за инструменти; 5 - стелаж за хоризонтално съхранение на пръти; 6 - шкаф за регулиране
Характерно за автоматичните секции е многомашинното обслужване и настройката на оборудването от настройчик. Следователно в автоматичните секции за пуфове не е оборудвано отделно работно място, а обектът като цяло. Описаната зона е оборудвана с монтажен шкаф (виж фиг. 12), приемни маси (виж фиг. 8, 10) и стелажи за съхранение на пръти (виж фиг. 10).
Приемащите маси са предназначени да поставят върху тях контейнери с готови части и измервателния инструмент, който е пряко необходим в работата (мери, шаблони и др.). Контейнерът с готови части се прехвърля на работното място на отдела за контрол на качеството с помощта на юра-лъч. Броят пръчки, необходими на работника за една смяна, се подава към машината преди началото на смяната. Пръчките се поставят върху стелажи, съставени от две или три секции, свързани една с друга. Местоположението на стелажите се определя от дизайна на оборудването и удобството за повторно пълнене на решетките в машината.
Една от приемните маси при група машини, обслужвани от един работник, има кутии за инструменти, в които работникът съхранява необходимите инструменти.
Организационно оборудване на работните места
Нощното шкафче е предназначено за съхранение на необходимите инструменти на работните места на операторите на машини, документация и продукти за грижа за оборудването.
Всяко отделение на нощното шкафче се затваря с вратичка и се разпределя за един работник. Отделенията разполагат с кутии за инструменти и рафтове за съхранение на документация, неудебелени аксесоари и приспособления, смазочници, почистващи материали и др.
Горният рафт на нощното шкафче може да бъде покрит с пластмаса. В скоби е закрепена подвижна плоча за закрепване на чертежи и технологичен процес, изработена от декоративна дървесно-ламинирана пластмаса.
Рецепционна маса
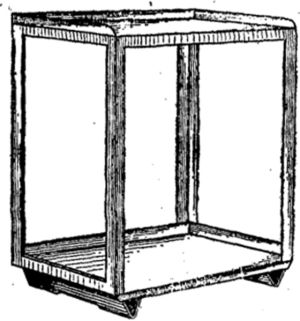
На горния рафт на масата има контейнер с обработени части или самите части. Ако е необходимо, приспособленията и аксесоарите могат да се съхраняват на долния рафт.
На отделни работни места масата може да се използва за поставяне на инструмента, използван в работата.
Поставка за аксесоари с изтегляща се платформа
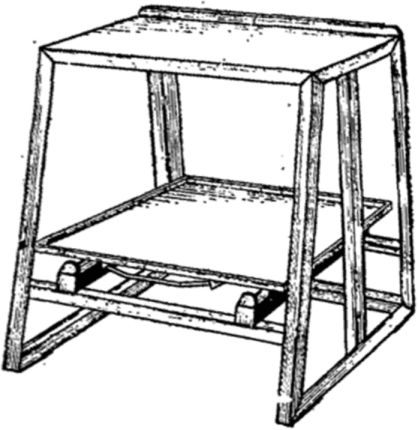
Платформата се движи на ролки и има ограничител на хода. Детайлите на стелажа са изработени от огънат профил и стоманена ламарина. Горният рафт и платформата са изработени от дърво, импрегнирано с фенолформалдехидна смола.
Рецепционна маса с кутии за инструменти
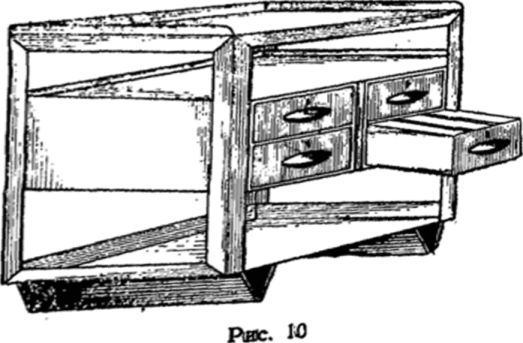
ЧЕКМЕДЖЕ НА БЮРОТО Използва се за съхранение на инструменти, а горният рафт за поставяне на контейнери с части или за подреждане на инструменти, необходими за работата.
Дизайнът предвижда възможност за инсталиране на две или четири * gyreh кутии за инструменти. При монтиране на четири чекмеджета, две от тях се поставят на закачалка с релси, прикрепени топки и стелажи.
Кутиите се движат лесно на ролки и имат ограничител на хода. те могат да бъдат инсталирани регулируеми прегради, образуващи клетки и желания размер. Между горния рафт и чекмеджетата има място за техническа документация. От задната страна на масата има скоби за монтаж на таблета за документация. Частите Olika са изработени от огънат профил и стоманена ламарина.
Мобилна приемна маса
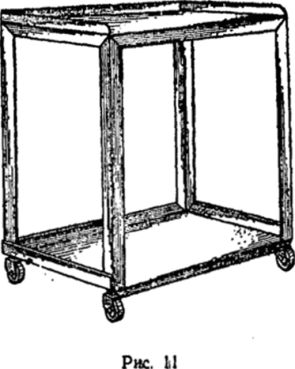
Масата се използва на тези работни мостове, където поради условията на работа стационарно офис оборудване (шкафове с инструменти или приемни маси) не може да се монтира достатъчно близо и удобно в близост до машината.
На горните и долните рафтове на масата работникът поставя инструмента, от който се нуждае в работата си, и поставя масата на най-удобното място за себе си. Детайлите на масата са изработени от огънат профил и стоманена ламарина. При необходимост масата може да бъде оборудвана с дръжка за по-лесно придвижване.
Гардероб

Ориз. Не.
Шкафът се състои от отделни елементи (основа, рамена и задни стекове, врати, чекмеджета и рафтове). Рафтовете могат да бъдат повторно stashp> но височина. Регулируемите прегради могат да се монтират в чекмеджета и на рафтове, образувайки клетки с желания размер. За да поставите дълъг инструмент в кухината на вратите, един. далечни държачи.
Рафтове за хоризонтално съхранение на барове
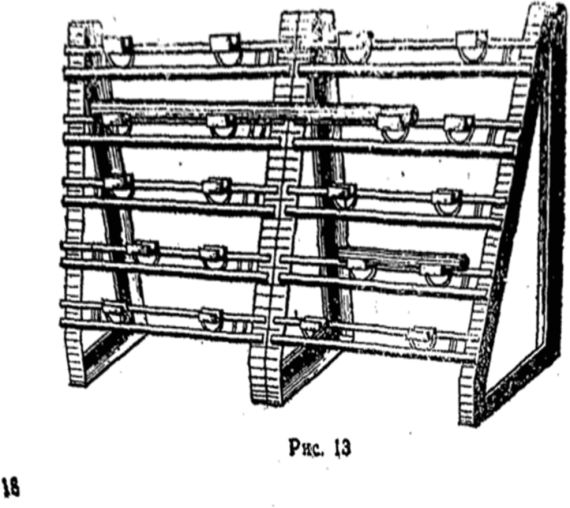
Стелажът има пет релси, разположени на различни височини, върху които са фиксирани мобилни опори.
Пръчките се полагат върху опори, чието местоположение и брой се определят за всеки отделен случай. Дизайнът предвижда възможност за свързване на стелажни секции по дължина. На фиг. 13 показва две секции, свързани една с друга.
Детайлите на стелажа са изработени от огънат профил и ъгъл. Носещата призма е изработена от дърво, импрегнирано с фенолформалдехидна смола.
2. Изчисляване на нормите на време
3. Изчисляване на режимите на обработка
Режимите на обработка трябва да се определят за всяка операция поотделно, разбити на преходи.
Параметри на режимите на обработка, които включват:
Обработка на детайли на металорежещи машини - издръжливост на инструмента, дълбочина на рязане, подаване, скорост на рязане, скорост на въртене на детайла (или инструмента), сила на рязане;
Заваряване (наваряване) ръчно с електродъга - вид, марка и диаметър на електрода, сила на заваръчния ток, поляритет;
Заваряване (наваряване) ръчно газово - номер на газовата горелка, вид на пламъка, марка на добавъчния материал, флюс;
Автоматично наваряване - сила на заваръчния ток, скорост на наваряване, стъпка на наваряване, височина на наплавения слой за едно минаване, позиция на заваръчния шев, добавъчен материал и др.;
Метализация - параметри на електрически ток, налягане и въздушен поток, разстояние от дюзата до детайла, час-тота на въртене на детайла, подаване и др.;
Галванично покритие - атомна маса, валентност, електрохимичен еквивалент, металоотдаване по ток, плътност и др.
Когато извършвате това изчисление, трябва да се съсредоточите върху намирането на компонентите за определяне на основното (машинно) време (T o).
Пример. Операция 06 обръщане
където L, - очаквана продължителност на обработката , mm, (ход на режещия инструмент)
аз-брой преминавания (обикновено i = I);
n, - скорост на шпиндела, rpm, (брой обороти на част или инструмент),
S - подаване на режещ инструмент mm/rev. Вижте L-3 за подробности.
В курсовия проект е необходимо да се определят нормите на време за предварително избраните 2 - 3 операции (обратно). Нормата на времето (T n) се определя, както следва:
T n \u003d T o + T в \u003d T допълнителен +
където T 0 е основното време (времето, през което се променя формата, размерът, структурата и т.н. на частта. Машинното време (To) се определя чрез изчисление);
T in - спомагателно време (времето, което осигурява изпълнението на основната работа, т.е. за монтаж, подравняване и отстраняване на детайла, завъртане на данните, измерване и т.н. (Tv) се определя от таблиците);
T допълнително - допълнително време (време за поддръжка на работното място, почивка за почивка и др.)
Където K е процентът на допълнителното време, взет съгласно табл. (Л-3, л.47, табл.7);
T p-z - подготвително - крайно време (Времето за получаване на задачата, запознаване с чертежа, настилка на инструмента и т.н. (T p-z) се определя от таблиците)
X - размерът на производствената партида от части (вижте раздел № 2 на това ръководство).
Трябва да знаете, че:
Където Tsht - време на парче.
За подробна информация относно определянето на Tn вижте L-3, o.12-15 и др.
Определянето на времеви дупки в курсовия проект (както и в контролната работа P) трябва да се извърши, както следва.
Пример 1. Определете времето на парче (Tsht) за струговане
резбова шийка на кормилния накрайник на автомобил ЗИЛ-431410 след напластяване.
Операция 06 обръщане. Обработката се извършва от D = 40 mm до
d = 36 mm на дължина l = 30 mm. Оборудване: винторежещ струг 1K62,
Изходни данни
1.1. Детайл - въртящ се юмрук, струговане с резба. вратове: D = 40; d=36; l = 30.
1.2. Материал - стомана, 40Х.
1.3. Твърдост - HB 241...285,
1.4. Теглото на частта е до 10 кг.
1.5. Оборудване - струг 1К62.
1.6. Режещият инструмент е проходен фреза с плоча T15K6.
1.7. Монтаж на частта - в центровете.
1.8. Условия на обработка - без охлаждане.
2.1. Поставете детайла в центъра.
2.2. Завъртете шията с резба.
2.3. Премахване на детайла.
3. Изчисляване на квоти ( ч) за обработка
h = = =2,0
4.1. Определете дължината на обработката ( Л)
L = l + y = 30 + 3,5 = 33,5 mm
където l = 30(дължина на шийката с резба) ;
y=3,5(стойността на разреза и превишението на фрезата, L-3, стр. 74, таблица 38).
4.2. Определете броя на преминаванията ( аз) :
i = = = 1,
където h = 2(разрешение за обработка),
T-дълбочина на рязане.
При грубо обработване е желателно да се премахне цялата надбавка с едно минаване, така че приемаме t=h=2
4.3. Определяме теоретичното (таблично) подаване на фреза ( С)
S= 0,4 - 0,5 мм/об(Л-3, о. 56, табл. 8.)
4.4. Определете действителното надлъжно подаване ( С
S= 0,43, мм/об.
4.5. Определете скоростта на рязане ( V) табличен.
V= 143, m/min(Л-З, стр. 57, табл. 11).
4.6. Коригиране Vкато се вземат предвид условията на обработка на детайла.
V= V . ДА СЕ . ДА СЕ . ДА СЕ . K \u003d 143. 1.44. 0,7. 1.0. 1,0 = 144,2 м/мин,
където K = 1,44(Л-З, стр. 57, табл. 12);
К = 0,7(- "- стр. 58, табл. 14);
К = 1,0(- "- стр. 59, раздел 15);
К = 1,0(- "- стр. 59, раздел 16).
4.7. Определете броя на оборотите на частта ( н)
n== = 1147,6 об./мин
4.8. Определете действителния брой обороти на частта ( н) според паспорта на машината (вижте приложението)
n= 1000 об/мин.
5. Изчисляване на нормите на време
5.1 определя основното време (до)
5.2 Определяне на допълнителното време (TV)
TV \u003d T set + T pr \u003d 0,48 + 0,7 \u003d 1,18, мин.
Където T set \u003d 0,48 min - времето за инсталиране и премахване на частта (L-3, стр. 77, раздел 43)
T pr \u003d 0,5-0,8 - времето, свързано с преминаването (L-3, таблица 44)
5.3 Определение за допълнително време (T add)
5.4 Определяне на работното време (Tsht)
Tsht \u003d To + TV + Tdop \u003d 0,08 + 1,18 + 0,16 \u003d 1,42 мин.
Tsht = 1,42 мин
Техническо регулиране на сондажните работи
Времева норма:
Tn \u003d To + Tv + Td +
Where To е основното време.
Където L е дължината на обработка, mm L = l + y
l е дължината на обработената повърхност съгласно детайлния чертеж; y - количеството на проникване и надхвърляне на свредлото (райбер, зенкер)
i е броят на преходите (или броят на отворите на една част);
Паспортна стойност на фуража, mm/rev.
Изберете подаването според таблиците, като вземете предвид материала на детайла, материала на режещата част на инструмента и необходимото покритие. Координирайте с паспортните данни на машината (вижте Приложението) Приемете според паспорта на машината (вижте Приложението)
P P - паспортна стойност на скоростта на шпиндела на машината (виж Приложението)
Изберете табличната стойност на скоростта на развитие
Задайте корекционен фактор;
K 1 - (K m) - в зависимост от материала на частта;
K 2 - (K mr) - в зависимост от материала на режещата част на инструмента
K 3 - (K x) - в зависимост от състоянието на повърхността
K 4 - (K oh) - в зависимост от наличието на охлаждане.
Коригирана скорост на рязане:
Изчисляване на скоростта на шпиндела на машината:
D - диаметър на инструмента, mm
Координирайте с паспортните данни на машината P P (вижте Приложението)
T в - спомагателен, мин
Спомагателно време за демонтаж и монтаж. Зависи от начина на монтаж и закрепване
Спомагателно време за преход
Спомагателно време за измерване. Зависи от вида на инструмента (вижте страници 58-60)
Назначава се при наличие на измервателни преходи;
Т g - допълнително време, мин
K е процентът на допълнителното време. За сондажни работи K = 6% (L-3, стр. 47, ст. 7)
Т п.з. - подготвително - заключително време, мин. Монтира се на партида от части, зависи от вида на обработката и метода на инсталиране на частта
X - Размерът на производствената партида на детайла
ПРИМЕР 2 Определете времето за пробиване на отвори за монтажни шпилки в главината на задното колело от диаметър d = 20,08 до D = 26 mm на дължина 20 м. Материал - чугун KCh-35. Оборудване вертикално - пробивна машина модел 2Н-135
Допълнителна информация:
Брой дупки - 6;
Свредло за режещ инструмент от стомана P9
1. Дълбочина на рязане
Брой проходи - един; брой отвори на детайла - 6.
2 Скорост мин./об.
(Л-3, стр. 66, табл. 28).
Според паспорта на машината = 0,56 мм / об. (Вижте прикачения файл)
3. Скорост на рязане m/min.
Таблична стойност \u003d 17 m / min (L-3, стр. 67, табл. 30)
Корекция на скоростта на рязане:
K m = 065 - в зависимост от материала, който се обработва;
K mr \u003d 1,00 - в зависимост от режещия материал
K x = 0,75 - в зависимост от състоянието на обработваната повърхност;
K oh = 1,0 - в зависимост от наличието на охлаждане.
Вижте L-3, стр. 57-59.
Регулирайте скоростта на рязане:
17 . 0,65. 1.0. 0,75. 1,0 = 8,28 (m/min)
4. Скорост на шпиндела на машината
Според паспорта на машината N p \u003d 90 (rpm), вижте приложението.
5. Очаквана дължина на обработка L p = l + y
y = 12 mm (L-3, p. 102, tab. 64)
L p \u003d 20 + 12 \u003d 32 mm.
6 Основно време, мин.
7. Време за поддръжка
0,10 + 5. 0,04 = 0,40 мин. (L-3, стр. 103, табл. 66)
8. Допълнително време
K \u003d 6% (L-3, стр. 47, таблица 7)
9. Време за парче
Tsht \u003d To + TV + Tg \u003d 3,81 + 1,50 + 0,32 \u003d 5,53
Техническо регулиране на фрезовата работа
Времево време:
Това е основното време, мин
Където L е дължината на обработка, mm. L = l + y
Sl - дължина на обработваната повърхност съгласно чертежа на детайла
Sy - количеството на подаване и надминаване зависи от вида на резбата
Si - чисти проходи (брой шлици или брой обработени повърхности)
Минутно подаване, mm / min (според паспорта на stonka)
Стойност на таблицата на подаването, mm / rev. Избира се, като се вземат предвид материала на детайла, материала на режещата част на инструмента, необходимата честота на обработка и вида на фрезоване.
Паспортна стойност на честотата на въртене rpm (вижте приложението)
Задайте корекционни фактори
Регулирайте скоростта на рязане
Определете изчислената стойност на скоростта на шпиндела на машината
D - диаметър на фриза, mm
Честотата на въртене трябва да бъде съгласувана с паспортните данни на машината n n . Изчисляване на стойността на минутното подаване
Координирайте минутното подаване с паспортните данни на машината (вижте приложението)
T in - спомагателното време се определя по таблиците, като се отчита времето за разрез и отстраняване на детайла, въртене и др.
Tdop - допълнително време.
Определя се по същия начин, както при предишните изчисления, като се вземе предвид K = 7% - за фрезови работи.
ПРИМЕР 3. Определете времето за фрезоване на шлиците на полуоската на автомобила. Гърлото на шлица след наваряване се обръща до диаметър 54 mm. Брой гнезда - 16, дължина - 85 мм, вътрешен диаметър - 46 мм. Оборудване - хоризонтално - фреза модел 6М82Г.
Допълнителна информация:
Материал на частта - стомана 45; = 700 MPa
Инструмент - дискова фреза с диаметър D f = 65 mm, брой зъби - 14, материал на фрезата - бързорежеща стомана R9
- Дълбочина на рязане
Брой преходи i = 16 (според броя на слотовете)
2. Подаване на оборот на ножа
3. Скорост на рязане, m/min. Табличен.
(L-3, p.10, tab.74)
4. Корекция на скоростта на рязане
Където K 1 \u003d 0,51 (L-3, стр. 57, таблица 12)
K 2 \u003d 0,7 (L-3, стр. 58, таблица 14)
K 3 \u003d 1.0 (L-3, стр. 59, табл. 15)
5. Скорост на шпиндела на машината
6. Минутна предавка, S m , mm/min.
Според паспорта на машината = 125 мм / мин. (Вижте прикачения файл)
7. Очаквана продължителност на обработката
L p \u003d l + y \u003d 85 + 17,5 \u003d 102,5 mm
Където l е дължината на слотовете;
y - увеличение на времето на ножа (l 1) и производителността на ножа (l 2) - превишаване;
l 1 = 15 (L-3, стр. 114, табл. 79)
l 2 = 2,5 (L-3, стр. 114, табл. 79)
8. Редовно време
9. Помощно време
T in \u003d T toy in + T pr in = 0,6 + 3,8 \u003d 4,4, мин.
Тоу в = 0,6 (L-3, л. 115, табл. 81).
T pr in \u003d 0,8 + 0,2. (n - 1) = 0,8 +0,2. (16 - 1) = 3,8,
Където n = 16 (брой слотове).
10. Допълнително време
T добавяне \u003d
Където K \u003d 7% (L-3, стр. 47, таблица 7).
11. Парче време
T бр \u003d T o + T in + T допълнително \u003d 13,12 + 4,40 + 1,23 \u003d 18,75, мин. Т бр = 18,75, мин.
Техническо регулиране на шлифовъчни работи.
Цилиндрично външно шлайфане с кръстосано подаване на двоен ход на масата
редовно време
където L p е дължината на хода на масата, когато кръгът излиза в двете посоки L p \u003d l + B
l - дължина на обработваната повърхност, mm
B - ширина (височина) на шлифовъчното колело, mm
Когато кръгът излезе в една посока L p \u003d l + B / 2
При смилане без напускане на кръга L p \u003d l - B
z - допустимото отклонение за всяка страна, mm
n и - скорост на въртене на детайла, об / мин
v и - скорост на продукта, m/min.
D - диаметър на детайла, mm
Свържете скоростта с данните на табелката на машината n и
S pr - надлъжно подаване, mm / rev
S t - дълбочина на смилане (напречно подаване)
K - коефициент, отчитащ износването на колелата и точността на смилане
K = 1,1-1,4 за грубо шлайфане
K = 1,5-1,8 за фино смилане
Външно цилиндрично шлайфане
S p - радиално подаване, mm/rev
Кръгло вътрешно шлайфане
L p \u003d l m - 1 / 3V - за проходни отвори
L p \u003d l m - 2 / 3V - за слепи отвори
Z - надбавка за обработка, mm
Цилиндрично безцентрово шлайфане с надлъжно подаване
l m - дължина на полиран продукт, mm
S pr.m - минутно надлъжно подаване mm / min
Кръгло безцентрово шлифоване
Jhd t vr \u003d 0,01-0,02 мин - време на потапяне
Z - надбавка за диаметър, mm
S ppm - напречно минутно подаване. мм/мин
Където S p - рационален трансфер mmob
П - честота на въртене на шлифовъчното колело, rpm
U cr - периферна скорост на кръга m / s
D - диаметър на кръга (Вземете D = 300 mm)
Определете времето за парче (T парчета) за фино шлайфане на шийката под външния лагер на кормилния кол на автомобила ZIL-431410. Надбавка за шлайфане 0,017 Оборудване - кръглошлайф модел 3B151. Дължина на врата l = 28, диаметър D = 39.997, d = 39980
1. Изходни данни
1.1 Детайл: Въртящ се шарнир на автомобил ЗИЛ - 431410. D = 39.997, d = 39980, l = 28, z = 0.017
Изчисляване на режими на обработка и времеви стандарти
L-4 дава препоръки за изчисляване на нормите за време за основните видове ремонтни работи с примери. Справочните данни са дадени съгласно справочника L-4. Това не изключва възможността за използване на друга справочна литература относно нормирането на ремонтните работи.
Техническо регулиране на стругарските работи
Времева норма:
където T o - основно време (машина),
L p - прогнозна дължина на обработка, mm. Определя се, като се вземе предвид вида на струговане (струговане, пробиване, режещи краища, набраздяване).
където l е дължината на обработената повърхност съгласно детайлния чертеж;
y е стойността на разреза и хода на фрезата;
i – брой преминавания (обикновено i=1);
S p около - паспортна стойност на фуража, mm / rev.
Изберете подаването S p o според таблиците, като вземете предвид материала на детайла, материала на режещата част на инструмента и необходимото покритие.
За обработка на грапави и непостоянни повърхности, намалете табличната стойност на подаване с 20-35%. Координирайте S p about с паспортните данни на машината (вижте Приложението). Вземете S p около = ... mm / rev.
N p - паспортна стойност на скоростта на шпиндела на машината;
изберете табличната стойност на скоростта на рязане V p t;
задайте коригиращи фактори:
K m - в зависимост от материала на детайла;
K mr - в зависимост от материала на режещата част на инструмента;
K x - в зависимост от състоянието на обработваната повърхност;
K oh - в зависимост от наличието на охлаждане;
Регулирайте скоростта на рязане:
V r ck \u003d V r t ∙K m ∙K mr ∙K x ∙K oh;
Определете изчислената стойност на скоростта на шпиндела на машината:
където D е диаметърът на детайла.
Координирайте с паспортните данни на машината n p.
T in - спомагателно време, мин.
T в \u003d T в su + T в pr + T в измервания, мин.
T in su - спомагателно време за монтаж и демонтаж на частта, зависи от начина на монтаж и закрепване;
Т в пр - спомагателно време за преминаване;
T in meas - спомагателно време за измервания, зависи от метода на измерване.
Назначава се, когато има преход на измерване.
T d - допълнително време, мин.
T d
където K е процентът на извънредния труд. За стругарски работи К=8%;
Т п.з. - подготвително и заключително време. Монтира се на партида от части, в зависимост от вида на обработката и начина на монтиране на частта;
P p - размерът на производствената партида части.
Пример 1Определете времето на детайла за завъртане на резбовата шийка след напластяване на оста на оста на автомобила ZIL-4314.10. Обработката се извършва от D=42 mm до D=36 mm при дължина l=32 mm. Оборудване: винторежещ струг 1К62.
Допълнителна информация:
Режещият инструмент е проходен фреза с твърдо топима плоча T5K10;
Обработен материал - стомана 40Х;
B c \u003d 400 MPa.
Решение:
1. Дълбочина на рязане
Брой преминавания i=1.
2. Подаване S, mm/rev. с грубо струговане и дълбочина на рязане t=3 mm и b c =400 MPa.
Стойност на таблицата S t \u003d 0,3-0,6 mm / rev.
Според паспорта на машината S p около =0,3 mm / rev.
3. Скорост на рязане V, m/min.
Стойност на таблицата V t \u003d 198 m / min.
Корекция на скоростта на рязане:
K m \u003d 1,65 - в зависимост от обработвания материал;
K mr \u003d 0,95 - в зависимост от материала на ножа;
K x \u003d 0,65 - в зависимост от състоянието на третираната повърхност;
K oh \u003d 1.0 - в зависимост от наличието на охлаждане.
Коригирана скорост на рязане:
V p ck \u003d 198 ∙ 1,65 ∙ 0,95 ∙ 0,65 ∙ 1,0 \u003d 201,74 m / min.
4. Скорост на въртене на частта n, rpm:
Според паспорта на машината n p \u003d 1600 rpm. (Вижте прикачения файл)
5. Очаквана продължителност на обработката
L p \u003d l + y \u003d 32 + 5 \u003d 37 mm,
където y=5 mm.
6. Основно (машинно време):
7. Помощно време.
2.8.1 Нормиране на операциите на универсални машини с ръчно управление.
Определяне на основното (технологично) време.
Основното време се определя по изчислителните формули за съответния вид работа и за всеки технологичен преход (T o1, T o2, ..., T o n).
Основното (технологично) време за операцията:
където n е броят на технологичните преходи.
Определение за спомагателно време.
За оборудване, предназначено за извършване на еднопреходна работа с постоянни режими в една операция (машини за многократно рязане, хидрокопиране, зъбонарязване, протягане, резбонарезни машини), се дава допълнителното време T за операцията, включително времето за инсталиране и демонтаж на детайл.
Спомагателното време за операцията се определя по формулата:
където t уста - времето за монтаж и демонтаж на детайла, дадено по вид на приспособлението, независимо от видовете машини, min;
t лента - времето, свързано с прехода, дадено по видове машини, min;
t' лента - време, което не е включено в комплекса от време, свързан с прехода, min;
t meas - време за контролни измервания след края на повърхностната обработка. Времето за контролни измервания се включва само в случаите, когато не се припокрива с основното време или не е включено в комплекса от време, свързан с прехода, min;
Kt in - корекционен коефициент за спомагателно време, мин.
Дефиниция на оперативно време:
, мин
където T около - основното време за обработка;
T in - спомагателно време за обработка, мин.
Определяне на време за поддръжка на работното място и лични нужди.
Времето за поддръжка на работното място, почивка и лични нужди се определя като процент от оперативното време съгласно нормативните справочници.
Стандартно време:
където α обс и α обн са времето за обслужване на работното място и времето за почивка и лични нужди, изразено в проценти от оперативното време.
Определяне на подготвително-заключително време.
Подготвителното и крайното време T pz се нормализира за партида части, като част от него за една част се включва във времето за изчисление на парчета:
, мин
където n d е броят на частите в партидата.
2.8.2 Нормализиране на операциите на универсални и многофункционални машини с ЦПУ.
Нормата на времето и неговите компоненти:
, мин
където T tsa - времето на цикъла на автоматична работа на машината според програмата, мин.
, мин
където T o - основното (технологично) време за обработка на една част се определя по формулата:
, мин
където L i е дължината на пътя, изминат от инструмента или детайла в посоката на подаване при обработка на i-тия технологичен участък (като се вземат предвид потапянето и превишаването), mm;
S mi - минутно подаване на i-тия технологичен участък, mm/min;
Tm-v - помощно време на машината според програмата (за подаване на детайл или инструмент от началните точки до зоните на обработка и прибиране, настройване на размера на инструмента, смяна на инструмент, промяна на големината и посоката на подаването), време на технологични паузи, мин.
, мин
където T v.y е времето за монтаж и демонтаж на частта ръчно или с асансьор, min;
T v.op - спомагателно време, свързано с операцията (не е включено в управляващата програма), min;
Т v.meas – спомагателно време без припокриване за измервания, min;
K t in - коефициент на корекция за времето за извършване на ръчна помощна работа, в зависимост от партидата детайли;
α тех., α орг., α отд - време за техническа, организационна поддръжка на работното място, за почивка и лични нужди за обслужване на едно гише, % от оперативното време.
Нормата на времето за настройка на машината се представя като време за подготвителна и окончателна работа по обработката на партиди от части, независимо от размера на партидата, и се определя по формулата:
където T p-31 - нормата на времето за получаване на поръчка, технологична документация в началото на работа и доставка в края на смяната, min; T p-31 = 12 минути;
T p-32 - нормата на времето за настройка на машина, приспособление, инструмент, софтуерни устройства, min;
T pr.arr - нормата на времето за пробна обработка (на първата част), мин.
Технически регламент.
Техническо нормиране се извършва за операция 005 „Струг с ПУ” и операция 030 „Комплексно с ПУ”.
1. Операция 005 "Струговане с ПУ".
1.1 Основното (технологично) време за обработка за всеки преход се определя по формулата:
, мин
, мин
където l cut - дължина на рязане, mm
y, ∆ - стойност на подаване или превишаване, mm
L е дължината на пътя на режещата част на инструмента, mm.
L 1 \u003d (113-70) / 2 + (65-33) / 2 + 4 \u003d 42 mm;
L 2 \u003d 35 + 5 +2 + 4 + 2,5 + 4 \u003d 57 mm;
L 3 \u003d (113-70) / 2 + 4 \u003d 11 mm;
L 4 \u003d 57 + 4 \u003d 61 mm;
L 5 \u003d 57 + 4 + 1 + 4 \u003d 66 mm.
T o1 \u003d 42 / (0,6 × 315) \u003d 0,22 min;
T o2 \u003d 51 / (0,6 × 500) \u003d 0,27 min;
T o3 \u003d 11 / (0,15 × 500) \u003d 0,14 min;
T o4 \u003d 61 / (0,3 × 800) \u003d 0,25 min;
До 5 \u003d 66 / (0,15 × 1250) \u003d 0,35 мин.
1.2 Основното време за обработка на операция се определя по формулата.