BUREAU CENTRAL DES NORMES DU TRAVAIL À L'INSTITUT DE RECHERCHE SCIENTIFIQUE DU TRAVAIL
COMITÉ D'ÉTAT DU CONSEIL DES MINISTRES DE L'URSS SUR LE TRAVAIL ET LES SALAIRES
Numéro III
FIXATIONS NORMALISÉES
Moscou - 1975
BUREAU CENTRAL DES NORMES DU TRAVAIL DE L'INSTITUT DE RECHERCHE SUR LE TRAVAIL DU COMITÉ D'ÉTAT DU CONSEIL DES MINISTRES DE L'URSS SUR LE TRAVAIL ET LES SALAIRES
DÉLAIS TYPIQUES DE CONSTRUCTION GÉNÉRALE DE MACHINES pour l'usinage de pièces de machines
Numéro 111 FIXATIONS NORMALISÉES
Normes générales de construction de machines de temps pour l'usinage de pièces de machines. Numéro III. Attaches normalisées
Les normes standard sont destinées aux évaluateurs, technologues et autres ingénieurs et techniciens impliqués dans l'élaboration de normes techniquement solides pour le traitement des fixations normalisées dans les ateliers (sites) de travail des métaux non spécialisés des entreprises.
Les normes de temps standard sont approuvées et recommandées pour utilisation dans les entreprises par la section du Conseil d'experts et de méthodologie de la Banque centrale de la science et de la technologie et approuvées par le Comité d'État du Conseil des ministres du travail et des salaires de l'URSS (décret n ° 208 du 15 août 1972) et en accord avec le Conseil central des syndicats de toute l'Union.
La collection a été développée par le Bureau central des normes du travail avec la participation d'entreprises et d'organismes de réglementation de divers ministères de la construction de machines.
Ces normes modèles sont une édition révisée et complétée des normes précédemment publiées et sont introduites pour remplacer la collection de l'édition 1964-1965.
La collection correspond à l'édition de 1975.
Veuillez envoyer tous les commentaires et suggestions sur cette collection à l'adresse : 103112, Moscou, KL2, pl. Kuibysheva, 1, TsBNT.
© Institut de recherche sur le travail du Comité d'État du Conseil des ministres de l'URSS sur le travail et les salaires (Institut de recherche sur le travail), 1975
UNE PARTIE COMMUNE
Ces normes de temps standard sont recommandées pour normaliser le travail des machines dans la fabrication de palans de fixation normalisés de machines dans des ateliers non spécialisés d'entreprises de construction de machines effectuées sur des tours, des tours, des perçages, des meulages et d'autres machines pour petites et grandes conditions de production de masse et sur tours automatiques monobroches - pour la production en série "et à grande échelle.
Lors du développement de cette collection, la nomenclature acceptée des pièces a été alignée sur les exigences des GOST nouvellement publiés et révisés.
Avec la révision des normes standard de l'édition de 1964, la collection a été considérablement élargie. De plus, les normes de temps pour le traitement des fixations sur les tours automatiques monobroches sont indiquées. La collection est complétée par des cartes pour le moletage et le calibrage des filets, le meulage des surfaces lisses, le traitement des broches, etc.
Les documents suivants sont à la base de l'élaboration des normes de temps standard :
1. Normes générales de construction de machines pour les modes de coupe pour la réglementation technique du travail sur les machines à couper les métaux. M., "Ingénierie", 1967.
2. Normes générales d'ingénierie pour le temps auxiliaire, pour l'entretien du lieu de travail et le temps préparatoire et final lors du travail sur des machines à couper les métaux (production à petite échelle et unique). M., Institut de recherche sur le travail, 1968.
3. Normes générales d'ingénierie pour le temps auxiliaire, pour l'entretien du lieu de travail et préparatoire et finale pour la réglementation technique du travail à la machine (production en série). M., Institut de recherche sur le travail, 1968.
4. Normes générales de construction de machines concernant le temps et les conditions de coupe pour les travaux de tournage automatique (production en série, à grande échelle et en série). M., "Ingénierie", 1971.
Lors de l'élaboration des normes de temps standard, ainsi que des normes générales de construction de machines ci-dessus, les éléments suivants ont été utilisés :
1. GOST pour les fixations (voir la liste des pièces à la page 20).
2. Processus technologiques, conditions de coupe utilisées dans les entreprises et observations chronométriques dans les conditions de production pour le temps consacré au traitement des fixations par machine-outil.
3. Délais de fabrication des attaches industrielles et locales.
4. Données de passeport pour l'équipement.
b. Les résultats d'analyse processus de travail, l'étude des méthodes rationnelles de travail et l'organisation du travail.
Les délais de collecte sont exprimés en minutes. Les limites des indicateurs numériques (longueur, diamètre, etc.) pour lesquelles "jusqu'à" est indiqué doivent être comprises inclusivement.
La collection de normes de temps standard comprend les sections suivantes :
Une partie commune ;
Caractéristiques de l'équipement utilisé et technologie de travail;
Organisation du Travail;
Partie réglementaire ;
Applications.
Les normes de temps typiques pour l'usinage des fixations sont un type d'élargissement complet, lorsque pour chaque opération les normes de temps de pièce et de préparation-finale sont données.
Pour la commodité d'utiliser la collection dans les cartes des normes standard, le temps est donné pour le traitement complet des pièces, et les options de traitement individuelles sont également mises en évidence.
Les durées de fonctionnement typiques incluent :
a) temps (technologique) principal ;
B) temps auxiliaire pour l'installation et le retrait de la pièce ;
c) temps auxiliaire associé à la transition ;
d) - temps d'entretien du poste de travail, de repos et de soins personnels (dans la limite de 5 à 10% du temps opérationnel, selon le type de travail).
Le temps partiel aux pièces comprend les mêmes composantes, à l'exception du temps auxiliaire pour l'installation et le démontage.
Préparatoire la dernière fois dans la collection est donnée en fonction des types de machines-outils (graphique 62). Ce temps, fixé pour un lot de pièces usinées, prévoit le périmètre de travail suivant :
1. Obtention d'une commande et d'une documentation technique.
2. Familiarisation avec le travail, les dessins et la réception des instructions du maître.
3. Obtention d'outils et d'accessoires, préparation du lieu de travail, mise en place d'équipements, d'outils et d'accessoires.
4. Enlèvement des outillages et outillages à la fin du traitement d'un lot de pièces, leur livraison.
5. Réajustement partiel des équipements en cours de travaux.
Les normes de temps typiques sont conçues pour des conditions organisationnelles et techniques correspondant au type de production accepté. La taille du lot de pièces pris comme un tout, et les facteurs de correction pour changement des conditions de travail sont donnés après les fiches de temps aux pièces par type de machine.
Pour les tours automatiques monobroches, le lot de pièces accepté est supérieur à 500 pièces.
Si la machine effectue systématiquement le même type d'opérations sur
4
le traitement de pièces structurellement similaires, temps à la pièce, donné dans ces normes standards, doit être corrigé du coefficient /("0,70.
Les délais typiques sont calculés pour compléter le travail avec une maintenance en une seule station. Dans le cas d'une maintenance multi-machines, il convient d'appliquer des normes standards avec des coefficients :
Le niveau de productivité du travail adopté dans les normes standard tient compte de l'expérience du travail des ateliers d'usinage des entreprises de construction de machines.
Dans les cas où les normes de temps en vigueur dans l'entreprise sont inférieures aux normes standard, ces normes de temps plus progressives ne doivent pas être augmentées.
Avec l'entrée en vigueur de ces normes modèles, la collection de l'édition de 1964 ou 1966 est annulée.
Lors de l'établissement de normes de temps dans les entreprises sur la base des normes de temps standard de cette collecte, la facturation du travail doit être effectuée conformément au tarif unifié et au livre de référence de qualification des travaux et des professions des travailleurs, numéro 2, approuvé par le décret de l'État Comité du Conseil des ministres de l'URSS sur le travail et les salaires et Conseil central des syndicats de toute l'Union n° 22 du 21 janvier 1969, sous réserve d'ajouts et de modifications ultérieurs.
L'écart entre les qualifications du travailleur et la catégorie de travail établie ne peut servir de base à aucune modification des normes de temps dans la collecte.
Caractéristiques des équipements utilisés et de la technologie
travailler
Les caractéristiques techniques des machines représentatives, données de passeport, qui ont été prises en compte lors du choix des conditions de coupe, sont présentées dans le tableau ci-dessous.
Les caractéristiques techniques et technologiques des modèles de machines-outils ci-dessus sont qu'ils disposent d'un ensemble complet d'avances, de vitesses et d'une puissance suffisante.
Type de machine |
Choix |
Puissance ■ k*t |
Limites de vitesse de mouvement principal en tr/min |
Limites de chute en mm/tr |
|||
Fraisage |
5 face avant |
Longitudinal transversal vertical |
|||||
longitudinal transversal vertical |
|||||||
Smolilny |
Diamètre de perçage maximal | ||||||
Krugloshlnfs-eal |
Diamètre de meulage maximal Longueur de broyage maximale |
pièce 30-235 |
Tableau des vitesses déplacées* en m/min 200 - 6000 Alimentation croisée de la poupée de meulage en un seul coup 0,01-0,02 ; 0,03-0,01 |
Continuation
Type Stayak" |
Choix |
Les limitations de vitesse du mouvement principal dans environ ! mime |
Limites d'avance en mm/tr |
||||
Machine à roulettes sans berceau |
Diamètre de ponçage |
le plus grand moins | |||||
longueur de la pièce à usiner |
|||||||
Machine semi-automatique de filetage à tête rotative | (coupe de boulons) | |||||||
Machine à fileter à rouleaux ronds A |
Le plus grand diamètre du fil à couper | ||||||
Tour monobroche ga tomate |
Le plus grand diamètre de traitement |
1150 - 7800 800-7670 550-3200 |
Les normes de temps typiques sont conçues pour les technologies suivantes dans les conditions suivantes :
L. Le temps à la pièce dans les cartes est défini pour le traitement de pièces en aciers au carbone de construction a * "60-76 kg / mm 2. Lors du traitement de pièces avec un outil en acier rapide, des coefficients sont fournis en fonction de la qualité du matériau traité. Lors de l'usinage de pièces à l'aide d'outils en carbure, des facteurs de correction sont donnés en fonction de la résistance du matériau à usiner.
B. Une pièce utilisée pour calculer le temps à la pièce lors du traitement de pièces sur des tours et des tours à tourelle, pour des pièces d'un diamètre allant jusqu'à 20 mm - une barre de 1000 mm de long, pour des pièces d'un diamètre supérieur à 20 mm - une pièce séparée de produits laminés, emboutis ou forgés. Lors de l'usinage de pièces sur des tours automatiques monobroches, une barre de 3000 mm de long est prise comme pièce à usiner.
3. L'installation des pièces est effectuée dans des fixations universelles.
4. Les modes de travail technologiques sur les tours et les tours à tourelle pour fraises sont conçus pour l'utilisation d'outils en carbure. Tous les autres types d'usinage (sauf meulage et roulage) sont réalisés avec un outil coupant en acier rapide. Pour le traitement automatique, les normes sont également calculées à condition d'utiliser un outil en acier rapide.
6. Les normes typiques pour le traitement des boulons, des vis et des écrous sur les tours et les tourelles sont calculées pour le filetage de la 3ème classe de précision. Dans le cas d'un filetage de 2ème classe, un facteur de correction /("U,2.
<6. В случае изготовления детали ко отдельной заготовки, штамповки или поковки время на отрезку не учитывалось.
7. Les délais de meulage sont calculés à condition de supprimer la surépaisseur de 0/1 mm par face.
8. Dans les normes de temps à la pièce, l'alignement des boulons et des vis est pris en compte pour leur traitement avec logement par le centre de la poupée mobile dans un rapport de la longueur de la pièce au diamètre de 8-<10 и рассверливание отверстий в гайках, начиная с диаметра резьбы 30 мм.
9. Lors de la coupe de filets sur des tours et des tourelles, l'utilisation de tarauds et de filières pour des diamètres allant jusqu'à 20 mm et de fraises pour des diamètres supérieurs à 20 mm est prise en compte dans les normes de temps à la pièce.
Organisation du travail
Avec une organisation rationnelle du travail, le lieu de travail doit être équipé conformément aux exigences du processus de production et aux conditions d'exécution du travail dans le respect des règles d'hygiène et de sécurité.
L'emplacement des équipements sur le lieu de travail, des stocks, du mobilier industriel, des conteneurs, des racks pour les ébauches et les produits finis est planifié de manière à éviter les conditions de travail exiguës, les coûts supplémentaires, le temps de marche et de recherche.
L'équipement du lieu de travail doit être suffisant et correct. L'éclairage requis est déterminé par la nature des travaux à effectuer et les normes sanitaires en vigueur.
En éclairage naturel et artificiel, il est recommandé de placer les postes de travail de manière à ce que la lumière tombe à gauche ou devant. En présence d'un éclairage local, la lumière ne doit pas aveugler les yeux, l'ombre ne doit pas tomber sur la pièce.
L'aménagement extérieur des lieux de travail et des locaux industriels doit répondre aux exigences de l'esthétique technique.
Le nombre d'outils et d'accessoires sur le lieu de travail doit être ". le minimum nécessaire pour assurer un fonctionnement ininterrompu pendant le quart de travail avec le moins de temps consacré à leur obtention et à leur remplacement.
Les outils et les accessoires doivent être situés sur le lieu de travail dans un certain ordre, pratique à utiliser.
Le nettoyage des copeaux et des déchets sur le lieu de travail est effectué par la production et les travailleurs, des lieux de travail - par les nettoyeurs des installations de production de l'atelier.
Le nombre de pièces à traiter, de pièces sur le lieu de travail est déterminé par le système d'organisation de la production et doit assurer un fonctionnement continu pendant le quart de travail.
Sur le lieu de travail, il existe une carte pédagogique et opérationnelle pour choisir l'érysipèle en coupe selon le type développé par l'usine Nevsky machine-cTpoH \ v .. oHWM nommée d'après. V. I. Lénine ou PKTImash (voir annexe 2).
Vous trouverez ci-dessous quelques schémas d'organisation des emplois pour les opérateurs de machines, en tenant compte des exigences d'organisation des travailleurs dans le comté.
Schéma d'organisation du poste de travail d'un tourneur

/ - table de chevet instrumentale; 2 - tablette pour accrocher des dessins; 3 - table de réception ; 4 - treillis pour les jambes
Le poste de travail du tourneur est équipé d'une armoire à outils pour le travail en deux équipes (voir Fig. 7), à chaque distance de laquelle est stocké un ensemble permanent d'outils et d'équipements pour l'entretien du matériel, ainsi qu'une table de réception (voir Fig. 8).
1 - table de chevet instrumentale; 2 - tablette pour accrocher des dessins de pièces; 3 - treillis pour les jambes; 4 - table de réception ; 5 - rack pour le stockage horizontal des barres
Le lieu de travail du revolver est équipé d'une armoire à outils installée à sa droite pour le travail en deux équipes (<см. рис. 7), приемным столиком (ом. рис. 8), установленным слева.
Un conteneur pour pièces finies est installé sur le plateau supérieur de la table de réception ; l'étagère inférieure peut stocker des accessoires pour la machine. Si (la machine à tourelle est conçue pour le traitement des barres et des cartouches, le conteneur en rack avec les ébauches est placé dans un endroit vide derrière l'armoire à outils. Pour les machines à tourelle destinées uniquement au traitement des mandrins, deux conteneurs sont installés sur la table de réception (pour les ébauches et pour les pièces finies); et le stock d'ébauches dans la stèle et le bac d'engraissement est situé à droite de l'ouvrier derrière l'armoire à outils.
Le poste de travail du foreur est équipé d'une armoire à outils pour le travail en deux équipes (voir Fig. 7), dans chaque compartiment duquel se trouve un ensemble permanent d'outils, et d'une table de réception (voir Fig. 8), placée à gauche. Sur l'étagère inférieure de la table de réception sont stockés de petits appareils.
Schéma d'organisation du lieu de travail d'un revolver

Schéma d'organisation du poste de travail d'un foreur travaillant sur une perceuse verticale
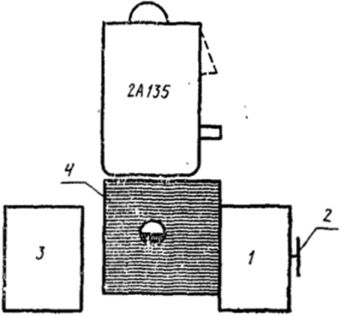
1 - armoire à outils. partager; 2 tablettes pour accrocher des dessins de pièces; 3 - table de réception ; grille de 4 pieds
L'ensemble d'outils nécessaires au travail direct est placé sur l'étagère supérieure de la table de chevet.
Schéma d'organisation du lieu de travail de la fraiseuse

/ - table de chevet instrumentale; 2-. plaque pour accrocher des dessins de pièces; 3 - table de réception ; 4 - treillis pour les jambes; 5 racks pour luminaires et accessoires ; 6 - râtelier pour mandrins et barres d'alésage
Le lieu de travail du meunier est équipé d'une armoire à outils pour le travail en deux équipes (om. Fig. 7), dans chaque compartiment dont un ensemble permanent d'outils était stocké.
La table de chevet est installée à droite du travailleur et une table de réception est placée à gauche (voir Fig. 8) pour deux conteneurs. Les accessoires et accessoires de la machine sont placés sur un rack avec une plate-forme coulissante (voir Fig. 9) installée derrière la machine.
Avec un stock accru de pièces destinées au traitement, celles-ci sont placées dans un conteneur rack ou sur des palettes à l'arrière de la machine.
Schéma d'organisation du lieu de travail du broyeur

1 - table de réception avec caisses à outils ; 2 - table d'accueil mobile ; 3 tablettes pour accrocher des dessins de pièces; Dispositif d'équilibrage à 4 pour un groupe de machines
Lorsque vous travaillez avec un outil abrasif, les règles de sécurité et d'hygiène industrielle ne permettent pas son stockage à long terme sur le lieu de travail, par conséquent, seuls les accessoires de la machine et un outil de mesure universel sont inclus dans l'ensemble permanent de l'outil de meulage.
Sur cette base, le lieu de travail du broyeur est équipé non pas d'une armoire à outils, mais d'une table de réception avec des boîtes à outils (le nombre de boîtes est déterminé dans chaque cas spécifique), dans laquelle un ensemble d'outils est stocké (voir Fig. dix).
Pour plus de commodité, le poste de travail du broyeur est équipé d'une table de réception mobile (voir Fig. III), sur laquelle est placé l'outil nécessaire au travail.
Schéma d'aménagement de la zone de traitement automatique
/ - tour monobroche 1A-Sh8; 2 - tour monobroche 1A124; 3 - table de réception ; 4 - "table de réception avec boîtes à outils; 5 racks pour le stockage horizontal des barres; 6 - armoire de réglage
La maintenance multi-machines et le réglage de l'équipement par un régleur sont typiques pour les sections automatiques. Par conséquent, dans les sections de bouffées automatiques, ce n'est pas un lieu de travail séparé qui est équipé, mais le site dans son ensemble. La zone décrite est équipée d'une armoire de monteur (voir Fig. 12), de tables de réception (voir Fig. 8, 10) et de casiers pour le stockage des barres (voir Fig. 10).
Les tables de réception sont conçues pour y placer des conteneurs avec des pièces finies et l'outil de mesure directement nécessaire au travail (jauges, gabarits, etc.). Le conteneur avec les pièces finies est transféré sur le lieu de travail du service de contrôle de la qualité à l'aide d'un faisceau yura. Le nombre de barres dont un travailleur a besoin pour un quart de travail est fourni à la machine avant le début du quart de travail. Les barres sont placées sur des râteliers constitués de deux ou trois sections reliées entre elles. L'emplacement des racks est déterminé par la conception de l'équipement et la commodité de remplir les barres dans la machine.
L'une des tables de réception d'un groupe de machines desservies par un travailleur comporte des boîtes à outils dans lesquelles le travailleur stocke les outils nécessaires.
Equipement organisationnel des lieux de travail
La table de chevet est conçue pour ranger les outils nécessaires sur les postes de travail des opérateurs de machines, la documentation et les produits d'entretien des équipements.
Chaque compartiment de la table de chevet est fermé par une porte et est attribué à un ouvrier. Les compartiments ont des boîtes à outils et des étagères pour ranger la documentation, les accessoires et accessoires non audacieux, les graisseurs, les produits de nettoyage, etc.
L'étagère supérieure de la table de chevet peut être recouverte de plastique. Une plaque amovible pour attacher des dessins et un procédé technologique, en plastique décoratif laminé bois, est fixée entre parenthèses.
Table de réception
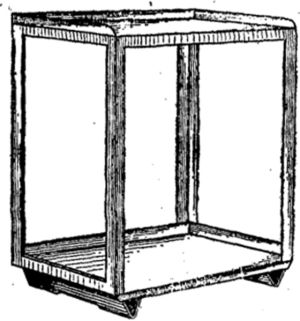
Sur l'étagère supérieure de la table se trouve un conteneur avec des pièces traitées ou les pièces elles-mêmes. Si nécessaire, les luminaires et les accessoires peuvent être rangés sur l'étagère inférieure.
Sur les lieux de travail individuels, la table peut être utilisée pour y placer l'outil utilisé dans le travail.
Porte-accessoires avec plate-forme coulissante
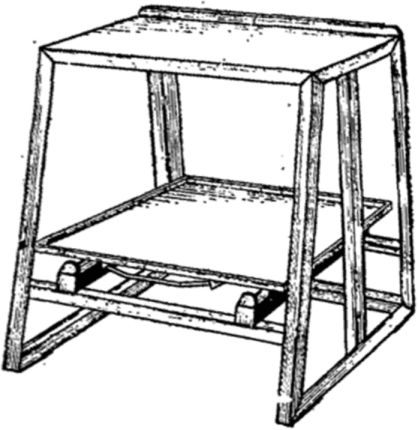
La plate-forme se déplace sur des rouleaux et dispose d'un limiteur de course. Les détails de la crémaillère sont constitués d'un profilé plié et d'une tôle d'acier. L'étagère supérieure et la plate-forme sont en bois imprégné de résine phénol-formaldéhyde.
Table de réception avec caisses à outils
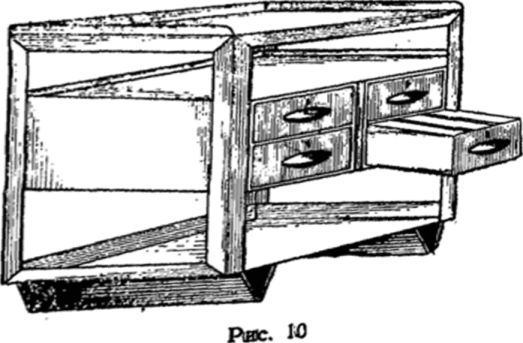
TIROIR DE BUREAU Utilisé pour ranger les outils et l'étagère supérieure pour placer des conteneurs avec des pièces ou pour disposer les outils nécessaires au travail.
La conception prévoit la possibilité d'installer deux ou quatre * boîtes à outils gyreh. Lors de l'installation de quatre tiroirs, deux d'entre eux sont placés sur un cintre avec des rails, des boules attachées et des supports.
Les caissons se déplacent facilement sur roulettes et disposent d'un limiteur de course. ils peuvent être installés des cloisons réglables, formant des cellules et la taille souhaitée. Entre l'étagère supérieure et les tiroirs, il y a de la place pour la documentation technique. Au dos de la table se trouvent des supports pour le montage sur la tablette de documentation. Les pièces Olika sont constituées de profilés pliés et de tôles d'acier.
Table d'accueil mobile
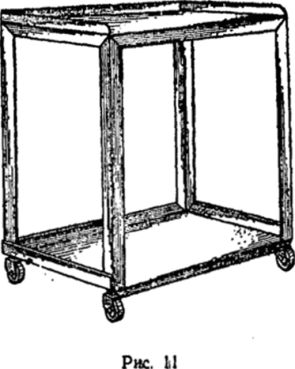
La table est utilisée sur les ponts de travail où, en raison des conditions de travail, les équipements de bureau fixes (armoires à outils ou tables de réception) ne peuvent pas être installés suffisamment près et commodément à proximité de la machine.
Sur les étagères supérieure et inférieure de la table, l'ouvrier dispose l'outil dont il a besoin dans son travail et place la table à l'endroit le plus pratique pour lui-même. Les détails de la table sont en profilé plié et en tôle d'acier. Si nécessaire, la table peut être équipée d'une poignée pour faciliter les déplacements.
Penderie

Riz. Non.
L'armoire se compose d'éléments individuels (base, flèche et piles arrière, portes, tiroirs de rangement et étagères). Les étagères peuvent être remises en place mais en hauteur. Des cloisons réglables peuvent être installées dans des tiroirs et sur des étagères, formant des cellules de la taille souhaitée. Pour loger un long outil dans la cavité des portes, un. détenteurs éloignés.
Rayonnage pour le stockage horizontal des barres
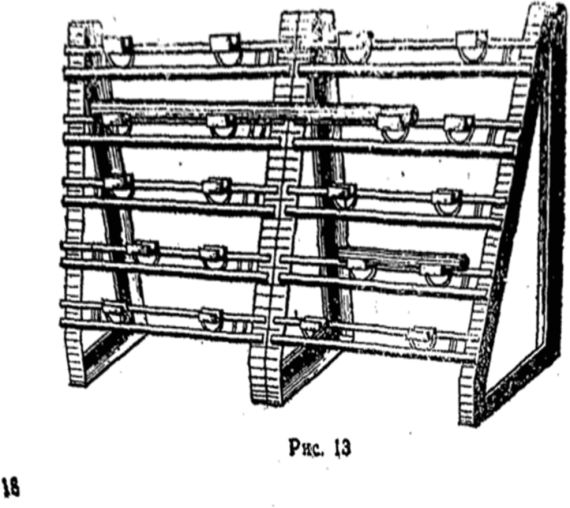
Le rack comporte cinq rails situés à différentes hauteurs, sur lesquels sont fixés des supports mobiles.
Les tiges sont posées sur des supports dont l'emplacement et le nombre sont déterminés dans chaque cas séparément. La conception prévoit la possibilité de connecter des sections de rack sur la longueur. Sur la fig. 13 montre deux tronçons reliés l'un à l'autre.
Les détails du rack sont constitués d'un profil plié et d'un coin. Le prisme de support est en bois imprégné de résine phénol-formaldéhyde.
2. Calcul des normes de temps
3. Calcul des modes de traitement
Les modes de traitement doivent être déterminés pour chaque opération séparément, décomposés en transitions.
Paramètres des modes de traitement qui incluent :
Usinage de pièces sur des machines à couper les métaux - durée de vie de l'outil, profondeur de coupe, avance, vitesse de coupe, vitesse de rotation de la pièce (ou de l'outil), puissance de coupe ;
Arc électrique manuel de soudage (surfaçage) - type, marque et diamètre de l'électrode, intensité du courant de soudage, polarité ;
Gaz manuel de soudage (surfaçage) - numéro de brûleur à gaz, type de flamme, marque de matériau d'apport, flux ;
Rechargement automatique - intensité du courant de soudage, vitesse de rechargement, étape de rechargement, hauteur de la couche déposée en un seul passage, position de la soudure, matériau de remplissage, etc. ;
Métallisation - paramètres du courant électrique, de la pression et du débit d'air, distance de la buse à la pièce, heure totale de rotation de la pièce, alimentation, etc. ;
Revêtement galvanique - masse atomique, valence, équivalent électrochimique, sortie de métal par courant, densité, etc.
Lors de ce calcul, vous devez vous concentrer sur la recherche des composants pour déterminer le temps principal (machine) (T o).
Exemple. Opération 06 tournage
où L, - durée estimée du traitement , mm, (course de l'outil de coupe)
je- nombre de passes (habituellement i = I);
n, - vitesse de broche, rpm, (nombre de tours d'une pièce ou d'un outil),
S - avance de l'outil de coupe mm/tr. Voir L-3 pour plus de détails.
Dans le projet de cours, il est nécessaire de déterminer les normes de temps pour les 2 à 3 opérations précédemment sélectionnées (ci-contre). La norme de temps (T n) est déterminée comme suit :
T n \u003d T o + T dans \u003d T supplémentaire +
où T 0 est le temps principal (le temps pendant lequel la forme, la taille, la structure, etc. de la pièce change. Le temps machine (To) est déterminé par calcul) ;
T in - temps auxiliaire (le temps qui assure l'exécution du travail principal, c'est-à-dire pour l'installation, l'alignement et le retrait de la pièce, le tournage des données, la mesure, etc. (Tv) est déterminé à partir des tableaux);
T supplémentaire - temps supplémentaire (temps pour l'entretien du lieu de travail, pause pour se reposer, etc.)
Où K est le pourcentage de temps supplémentaire, pris selon le tableau. (L-3, p.47, tableau 7) ;
T p-z - préparatoire - temps final (le temps pour recevoir la tâche, se familiariser avec le dessin, le surfaçage de l'outil, etc. (T p-z) est déterminé par les tableaux)
X - la taille du lot de production de pièces (voir la section n ° 2 de ce manuel).
Vous devez savoir que :
Où Tsht - temps à la pièce.
Pour des informations détaillées sur la détermination de Tn, voir L-3, o.12-15, etc.
La définition des trous temporels dans le projet de cours (ainsi que dans le travail de contrôle P) doit être effectuée comme suit.
Exemple 1. Déterminer le temps à la pièce (Tsht) pour le tournage
col fileté du porte-fusée d'une voiture ZIL-431410 après avoir fait surface.
Opération 06 tournage. L'usinage s'effectue de D = 40 mm à
d = 36 mm sur longueur l = 30 mm. Equipement : tour à décolleter 1K62,
Donnée initiale
1.1. Détail - poing pivotant, tournant fileté. cols : D = 40 ; d=36 ; l = 30.
1.2. Matériau - acier, 40X.
1.3. Dureté - HB 241...285,
1.4. Le poids de la pièce peut aller jusqu'à 10 kg.
1.5. Equipement - tour à décolleter 1K62.
1.6. L'outil de coupe est une fraise traversante avec une plaque T15K6.
1.7. Installation de la pièce - dans les centres.
1.8. Conditions de traitement - sans refroidissement.
2.1. Placez la pièce au centre.
2.2. Tourner le col fileté.
2.3. Supprimer le détail.
3. Calcul des indemnités ( h) pour traitement
h = = =2.0
4.1. Déterminer la durée de traitement ( L)
L = l + y = 30 + 3,5 = 33,5 mm
où l = 30(longueur du col fileté) ;
y=3.5(la valeur de la coupe et du dépassement de la fraise, L-3, p. 74, tableau 38).
4.2. Déterminer le nombre de passages ( je) :
je = = = 1 ,
où h = 2(indemnité de transformation),
t- profondeur de coupe.
Lors de l'ébauche, il est souhaitable d'éliminer toute la surépaisseur en une seule passe, nous acceptons donc t=h=2
4.3. Nous déterminons l'avance théorique (tabulaire) de la fraise ( S)
S= 0,4 - 0,5 mm/tour(L-3, o. 56, tab. 8.)
4.4. Déterminer l'avance longitudinale réelle ( S
S= 0,43, mm/tr.
4.5. Déterminer la vitesse de coupe ( V) tabulaire.
V= 143, m/min(L-Z, p. 57, tab. 11).
4.6. Correction V en tenant compte des conditions de traitement de la pièce.
V= V . À . À . À . K \u003d 143. 1.44. 0,7. 1.0 . 1,0 = 144,2 m/min,
où K = 1,44(L-Z, p. 57, tab. 12);
K = 0,7(- "- p. 58, tableau. 14);
K = 1,0(- "- p. 59, tab. 15);
K = 1,0(- "- p. 59, tab. 16).
4.7. Déterminer le nombre de tours de la pièce ( n)
n== = 1147,6 tr/min
4.8. Déterminer le nombre réel de tours de la pièce ( n) selon le passeport de la machine (voir annexe)
n= 1000 tr/min.
5. Calcul des normes de temps
5.1 déterminer l'heure principale (To)
5.2 Déterminer le temps auxiliaire (TV)
TV \u003d T ensemble + T pr \u003d 0,48 + 0,7 \u003d 1,18, min
Où T défini \u003d 0,48 min - le temps d'installation et de retrait de la pièce (L-3, p. 77, tab. 43)
T pr \u003d 0,5-0,8 - temps associé au passage (L-3, tableau. 44)
5.3 Définition des prolongations (T add)
5.4 Détermination du temps à la pièce (Tsht)
Tsht \u003d To + TV + Tdop \u003d 0,08 + 1,18 + 0,16 \u003d 1,42 min
Tsht = 1,42 min
Règlement technique des travaux de forage
Norme de temps :
Tn \u003d À + Tv + Td +
Where To est l'heure principale.
Où L est la longueur de traitement, mm L = l + y
l est la longueur de la surface usinée selon le dessin de détail ; y - la quantité de pénétration et de dépassement du foret (alésoir, fraisage)
i est le nombre de transitions (ou le nombre de trous sur une pièce) ;
Valeur passeport de l'alimentation, mm/tr.
Sélectionnez l'avance selon les tableaux, en tenant compte du matériau de la pièce, du matériau de la partie coupante de l'outil et de la finition requise. Coordonner avec les données de passeport de la machine (voir annexe) Accepter selon le passeport de la machine (voir annexe)
P P - valeur passeport de la vitesse de broche de la machine (voir annexe)
Sélectionnez la valeur tabulaire du taux de développement
Attribuez un facteur de correction ;
K 1 - (K m) - selon le matériau de la pièce;
K 2 - (K mr) - en fonction du matériau de la partie coupante de l'outil
K 3 - (K x) - en fonction de l'état de la surface
K 4 - (K oh) - en fonction de la présence de refroidissement.
Vitesse de coupe corrigée :
Calcul de la vitesse de broche de la machine :
D - diamètre de l'outil, mm
Coordonner avec les données de passeport de la machine P P (voir annexe)
T in - auxiliaire, min
Temps auxiliaire pour l'enlèvement et l'installation. Dépend de la méthode d'installation et de fixation
Temps de transition auxiliaire
Temps auxiliaire pour la mesure. Dépend du type d'outil (voir pages 58-60)
Attribué en présence de transitions de mesure ;
Т g - temps supplémentaire, min
K est le pourcentage de temps supplémentaire. Pour les travaux de forage K = 6% (L-3, p. 47, v. 7)
T p.z. - préparatoire - temps final, min. Installé sur un lot de pièces, dépend du type de traitement et de la méthode d'installation de la pièce
X - La taille du lot de production de la pièce
EXEMPLE 2 Déterminer le temps à la pièce pour percer les trous pour les goujons de fixation dans le moyeu de la roue arrière d'un diamètre de d = 20,08 à D = 26 mm sur une longueur de 20 m Matériau - Fonte KCh-35. Equipement vertical - perceuse modèle 2H-135
Informations Complémentaires:
Nombre de trous - 6 ;
Outil de coupe perceuse en acier P9
1. Profondeur de coupe
Nombre de passages - un ; nombre de trous sur la pièce - 6.
2 Vitesse min/tr.
(L-3, p. 66, tab. 28).
Selon le passeport de la machine = 0,56 mm/tr. (voir pièce jointe)
3. Vitesse de coupe m/min.
Valeur tabulaire \u003d 17 m / min (L-3, p. 67, tab. 30)
Correction de la vitesse de coupe :
K m = 065 - selon le matériau traité;
K mr \u003d 1,00 - selon le matériau de coupe
K x = 0,75 - selon l'état de la surface traitée ;
K oh = 1,0 - en fonction de la présence de refroidissement.
Voir L-3, p. 57-59.
Ajuster la vitesse de coupe :
17 . 0,65. 1.0 . 0,75. 1,0 = 8,28 (m/min)
4. Vitesse de broche de la machine
Selon le passeport de la machine N p \u003d 90 (rpm), voir l'annexe.
5. Durée de traitement estimée L p = l + y
y = 12 mm (L-3, p. 102, tab. 64)
L p \u003d 20 + 12 \u003d 32 mm.
6 Heure principale, min,
7. Temps d'assistance
0,10 + 5 . 0,04 = 0,40 min (L-3, p. 103, tab. 66)
8. Temps supplémentaire
K \u003d 6% (L-3, p. 47, tableau 7)
9. Temps à la pièce
Tsht \u003d To + TV + Tg \u003d 3,81 + 1,50 + 0,32 \u003d 5,53
Réglementation technique des travaux de fraisage
Nom du temps :
C'est l'heure principale, min
Où L est la longueur de traitement, mm. L = l + y
Sl - longueur de la surface usinée selon le dessin de détail
Sy - la quantité d'alimentation et de dépassement dépend du type de fil
Si - passes pures (nombre de cannelures ou nombre de surfaces usinées)
Avance minute, mm / min (selon le passeport stonka)
Valeur de table d'avance, mm / tour. Il est sélectionné en tenant compte du matériau de la pièce, du matériau de la partie coupante de l'outil, de la fréquence de traitement requise et du type de fraisage.
Valeur passeport de la fréquence de rotation rpm (voir annexe)
Attribuer des facteurs de correction
Ajuster la vitesse de coupe
Déterminer la valeur calculée de la vitesse de broche de la machine
D - diamètre de la frise, mm
La fréquence de rotation doit être coordonnée avec les données de passeport de la machine n n . Calcul de la valeur de l'avance minute
Coordonner l'alimentation minute avec les données de passeport de la machine (voir annexe)
T in - le temps auxiliaire est déterminé selon les tableaux, en tenant compte du temps pour la section et le retrait de la pièce, la rotation, etc.
Tdop - temps supplémentaire.
Il est déterminé de la même manière que dans les calculs précédents, en tenant compte de K = 7% - pour les travaux de fraisage.
EXEMPLE 3. Déterminer le temps à la pièce pour fraiser les cannelures de l'arbre d'essieu de la voiture. Le col cannelé après surfaçage est tourné à un diamètre de 54 mm. Nombre de fentes - 16, longueur - 85 mm, diamètre intérieur - 46 mm. Equipement - horizontalement - fraiseuse modèle 6M82G.
Informations Complémentaires:
Matériau de la pièce - acier 45 ; = 700 MPa
Outil - fraise à disque de diamètre D f = 65 mm, nombre de dents - 14, matériau de coupe - acier rapide R9
- Profondeur de coupe
Nombre de transitions i = 16 (selon le nombre de slots)
2. Avance par tour de fraise
3. Vitesse de coupe, m/min. Tabulaire.
(L-3, p.10, tab.74)
4. Correction de la vitesse de coupe
Où K 1 \u003d 0,51 (L-3, p. 57, tableau 12)
K 2 \u003d 0,7 (L-3, p. 58, tableau 14)
K 3 \u003d 1,0 (L-3, p. 59, tab. 15)
5. Vitesse de broche de la machine
6. Pignon des minutes, S m , mm/min.
Selon le passeport de la machine = 125 mm/min. (voir pièce jointe)
7. Durée estimée du traitement
L p \u003d l + y \u003d 85 + 17,5 \u003d 102,5 mm
Où l est la longueur des fentes ;
y - augmentation du temps de coupe (l 1) et de la puissance de coupe (l 2) - dépassement ;
l 1 = 15 (L-3, p. 114, tab. 79)
l 2 = 2,5 (L-3, p. 114, tab. 79)
8. Temps réglementaire
9. Temps auxiliaire
T en \u003d T oy en + T pr en \u003d 0,6 + 3,8 \u003d 4,4, min.
Тоу в = 0,6 (L-3, p. 115, tab. 81).
Tpr dans \u003d 0,8 + 0,2. (n - 1) = 0,8 +0,2 . (16 - 1) = 3,8,
Où n = 16 (nombre de slots).
10. Temps supplémentaire
T ajouter \u003d
Où K \u003d 7% (L-3, p. 47, tableau 7).
11. Temps à la pièce
T pcs \u003d T o + T in + T supplémentaire \u003d 13,12 + 4,40 + 1,23 \u003d 18,75, min. T pièces = 18,75, min.
Règlement technique des travaux de meulage.
Rectification extérieure cylindrique avec avance transversale sur double course de table
temps régulier
où L p est la longueur du trait de table lorsque le cercle sort dans les deux sens L p \u003d l + B
l - longueur de la surface traitée, mm
B - largeur (hauteur) de la meule, mm
Lorsque le cercle sort dans une direction L p \u003d l + B / 2
Lors du meulage sans quitter le cercle L p \u003d l - B
z - surépaisseur d'usinage par côté, mm
n et - vitesse de rotation de la pièce, tr/min
v et - vitesse du produit, m/min.
D - diamètre de la pièce, mm
Faites correspondre la vitesse avec les données de la plaque signalétique de la machine n et
S pr - avance longitudinale, mm / tour
S t - profondeur de meulage (alimentation transversale)
K - coefficient tenant compte de l'usure de la meule et de la précision de meulage
K = 1,1-1,4 pour le meulage grossier
K = 1,5-1,8 pour le meulage fin
Rectification cylindrique extérieure en plongée
S p - avance radiale, mm/tr
Rectification intérieure ronde
L p \u003d l m - 1 / 3V - pour trous traversants
L p \u003d l m - 2 / 3V - pour trous borgnes
Z - surépaisseur d'usinage, mm
Rectification centerless cylindrique avec avance longitudinale
l m - longueur du produit poli, mm
S pr.m - avance longitudinale minute mm / min
Rectification plongeante ronde sans centre
Jhd t vr \u003d 0,01-0,02 min - temps de plongée
Z - tolérance pour le diamètre, mm
S ppm - alimentation minute transversale. millimètre/minute
Où S p - transfert rationnel mmob
П - fréquence de rotation de la meule, tr/min
U cr - vitesse circonférentielle du cercle m / s
D - diamètre du cercle (Prenez D = 300 mm)
Déterminez le temps à la pièce (pièces en T) pour le meulage fin du cou sous le roulement extérieur du porte-fusée de la voiture ZIL-431410. Allocation de meulage 0,017 Equipement - rectifieuse circulaire modèle 3B151. Longueur du col l = 28, diamètre D = 39.997, d = 39980
1. Données initiales
1.1 Détail : Charnière pivotante d'une voiture ZIL - 431410. D = 39,997, d = 39980, l = 28, z = 0,017
Calcul des modes de traitement et des normes de temps
L-4 fournit des recommandations pour le calcul des normes de temps pour les principaux types de travaux de réparation avec des exemples. Les données de référence sont données selon le livre de référence L-4. Cela n'exclut pas la possibilité d'utiliser d'autres ouvrages de référence sur le rationnement des travaux de réparation.
Règlement technique des travaux de tournage
Norme de temps :
où T o - temps principal (machine),
L p - durée estimée du traitement, mm. Il est déterminé en tenant compte du type de tournage (tournage, alésage, coupe d'extrémités, rainurage).
où l est la longueur de la surface usinée selon le dessin de détail ;
y est la valeur de la coupe et du parcours de la fraise ;
i – nombre de passages (habituellement i=1) ;
S p about - valeur de passeport de l'alimentation, mm / tour.
Sélectionnez l'avance S p o selon les tableaux, en tenant compte du matériau de la pièce, du matériau de la partie coupante de l'outil et de la finition requise.
Pour le traitement de surfaces rugueuses et intermittentes, réduisez la valeur d'alimentation tabulaire de 20 à 35 %. Coordonnez S p about avec les données de passeport de la machine (voir annexe). Prenez S p environ = ... mm / tour.
N p - valeur passeport de la vitesse de broche de la machine;
sélectionner la valeur tabulaire de la vitesse de coupe V p t ;
attribuer des facteurs de correction :
K m - en fonction du matériau de la pièce;
K mr - en fonction du matériau de la partie coupante de l'outil;
K x - en fonction de l'état de la surface traitée ;
K oh - en fonction de la disponibilité du refroidissement ;
Ajuster la vitesse de coupe :
V r ck \u003d V r t ∙K m ∙K mr ∙K x ∙K oh;
Déterminez la valeur calculée de la vitesse de broche de la machine :
où D est le diamètre de la pièce.
Coordonner avec les données de passeport de la machine n p.
T in - temps auxiliaire, min.
T en \u003d T en su + T en pr + T en meas, min.
T in su - temps auxiliaire pour l'installation et le retrait de la pièce, dépend de la méthode d'installation et de fixation;
T in pr - temps auxiliaire pour le passage;
T in meas - temps auxiliaire pour les mesures, dépend de la méthode de mesure.
Attribué lorsqu'il y a une transition de mesure.
T d - temps supplémentaire, min.
T d
où K est le pourcentage d'heures supplémentaires. Pour travaux de tournage K=8%;
T p.z. - temps préparatoire et final. Il est installé sur un lot de pièces, en fonction du type de traitement et de la méthode d'installation de la pièce ;
P p - la taille du lot de production de pièces.
Exemple 1 Déterminez le temps à la pièce pour tourner le col fileté après avoir fait surface au niveau de la fusée d'essieu de la voiture ZIL-4314.10. L'usinage s'effectue de D=42 mm à D=36 mm à une longueur de l=32 mm. Equipement : tour à décolleter 1K62.
Informations Complémentaires:
L'outil de coupe est une fraise traversante avec une plaque à fusion dure T5K10;
Matériau traité - acier 40X ;
B c \u003d 400 MPa.
La solution:
1. Profondeur de coupe
Nombre de passages i=1.
2. Avance S, mm/tr. avec tournage grossier et profondeur de coupe t=3 mm et b c =400 MPa.
Valeur du tableau S t \u003d 0,3-0,6 mm / tour.
Selon le passeport de la machine S p environ = 0,3 mm / tour.
3. Vitesse de coupe V, m/min.
Valeur du tableau V t \u003d 198 m / min.
Correction de la vitesse de coupe :
K m \u003d 1,65 - en fonction du matériau traité;
K mr \u003d 0,95 - selon le matériau de la fraise;
K x \u003d 0,65 - selon l'état de la surface traitée;
K oh \u003d 1,0 - en fonction de la présence de refroidissement.
Vitesse de coupe corrigée :
V p ck \u003d 198 ∙ 1,65 ∙ 0,95 ∙ 0,65 ∙ 1,0 \u003d 201,74 m/min.
4. Vitesse de rotation de la pièce n, rpm :
Selon le passeport de la machine n p \u003d 1600 tr/min. (voir pièce jointe)
5. Durée estimée du traitement
L p \u003d l + y \u003d 32 + 5 \u003d 37 mm,
où y = 5 mm.
6. Principal (temps machine) :
7. Temps auxiliaire.
2.8.1 Rationnement des opérations sur machines universelles à commande manuelle.
Définition du temps principal (technologique).
Le temps principal est déterminé par les formules de calcul pour le type de travail correspondant et pour chaque transition technologique (T o1, T o2, ..., T o n).
Le temps principal (technologique) pour l'opération:
où n est le nombre de transitions technologiques.
Définition du temps auxiliaire.
Pour les équipements destinés à effectuer un travail à transition unique avec des modes constants en une seule opération (machines à taillage multiple, hydrocoping, taillage d'engrenages, brochage, filetage), le temps auxiliaire T est donné pour l'opération, y compris le temps de montage et de démontage des pièce.
Le temps auxiliaire pour l'opération est déterminé par la formule :
où t bouche - le temps d'installation et de retrait de la pièce, donné par type d'appareil, quels que soient les types de machines, min;
t voie - le temps associé à la transition, donné par les types de machines, min ;
t' voie - temps non inclus dans le complexe de temps associé à la transition, min ;
t mes - temps pour les mesures de contrôle après la fin du traitement de surface. Le temps des mesures de contrôle n'est inclus que dans les cas où il n'est pas recouvert par le temps principal ou n'est pas inclus dans le complexe de temps associé à la transition, min ;
Kt in - facteur de correction pour le temps auxiliaire, min.
Définition du temps opérationnel :
, min
où T environ - le temps principal de traitement;
T in - temps auxiliaire pour le traitement, min.
Détermination du temps pour l'entretien du lieu de travail et des besoins personnels.
Le temps pour l'entretien du lieu de travail, le repos et les besoins personnels est déterminé en pourcentage du temps opérationnel selon les ouvrages de référence normatifs.
Heure normale :
où α obs et α voln sont le temps d'entretien du lieu de travail et le temps de repos et de besoins personnels, exprimés en pourcentage du temps de fonctionnement.
Définition du temps préparatoire-finale.
Le temps préparatoire et final T pz est normalisé pour un lot de pièces, et une partie de celui-ci par pièce est incluse dans le temps de calcul de la pièce :
, min
où n d est le nombre de pièces dans le lot.
2.8.2 Normalisation des opérations sur les machines CNC universelles et polyvalentes.
La norme du temps et ses composantes :
, min
où T tsa - le temps de cycle du fonctionnement automatique de la machine selon le programme, min.
, min
où T o - le temps principal (technologique) de traitement d'une pièce est déterminé par la formule:
, min
où L i est la longueur du trajet parcouru par l'outil ou la pièce dans le sens de l'avance lors du traitement de la ième section technologique (en tenant compte de la plongée et du dépassement), mm;
S mi - avance minute sur la ième section technologique, mm/min ;
Tm-v - temps auxiliaire de la machine selon le programme (pour fournir une pièce ou un outil des points de départ aux zones de traitement et à la rétraction, régler l'outil sur une taille, changer un outil, changer la grandeur et le sens de l'avance), le temps de pauses technologiques, min.
, min
où T v.y est le temps de pose et de dépose de la pièce manuellement ou avec un ascenseur, min ;
T v.op - temps auxiliaire associé à l'opération (non inclus dans le programme de contrôle), min;
Т v.meas – temps auxiliaire sans chevauchement pour les mesures, min;
K t in - facteur de correction pour le temps d'exécution des travaux auxiliaires manuels, en fonction du lot de pièces;
α tech, α org, α otd - temps pour l'entretien technique et organisationnel du lieu de travail, pour le repos et les besoins personnels pour un service à guichet unique, % du temps opérationnel.
La norme de temps pour la mise en place de la machine est présentée comme le temps de travail préparatoire et final sur le traitement des lots de pièces, quelle que soit la taille du lot, et est déterminée par la formule :
où T p-31 - la norme de temps pour recevoir une commande, la documentation technologique au début du travail et la livraison à la fin du quart de travail, min; T p-31 = 12 min ;
T p-32 - la norme de temps pour la configuration d'une machine, d'un appareil, d'un outil, de dispositifs logiciels, min;
T pr.arr - la norme de temps pour le traitement du procès (de la première partie), min.
Règlement technique.
La normalisation technique est effectuée pour l'opération 005 "Tour avec PU" et l'opération 030 "Complexe avec PU".
1. Opération 005 "Tournage avec PU".
1.1 Le temps de traitement principal (technologique) pour chaque transition est déterminé par la formule :
, min
, min
où l coupe - longueur de coupe, mm
y, ∆ - valeur de pénétration ou de dépassement, mm
L est la longueur du trajet de la partie coupante de l'outil, mm.
L 1 \u003d (113-70) / 2 + (65-33) / 2 + 4 \u003d 42 mm;
L 2 \u003d 35 + 5 +2 + 4 + 2,5 + 4 \u003d 57 mm;
L 3 \u003d (113-70) / 2 + 4 \u003d 11 mm;
L 4 \u003d 57 + 4 \u003d 61 mm;
L 5 \u003d 57 + 4 + 1 + 4 \u003d 66 mm.
T o1 \u003d 42 / (0,6 × 315) \u003d 0,22 min;
T o2 \u003d 51 / (0,6 × 500) \u003d 0,27 min;
T o3 \u003d 11 / (0,15 × 500) \u003d 0,14 min;
T o4 \u003d 61 / (0,3 × 800) \u003d 0,25 min;
À 5 \u003d 66 / (0,15 × 1250) \u003d 0,35 min.
1.2 Le temps de traitement principal par opération est déterminé par la formule.